Contents
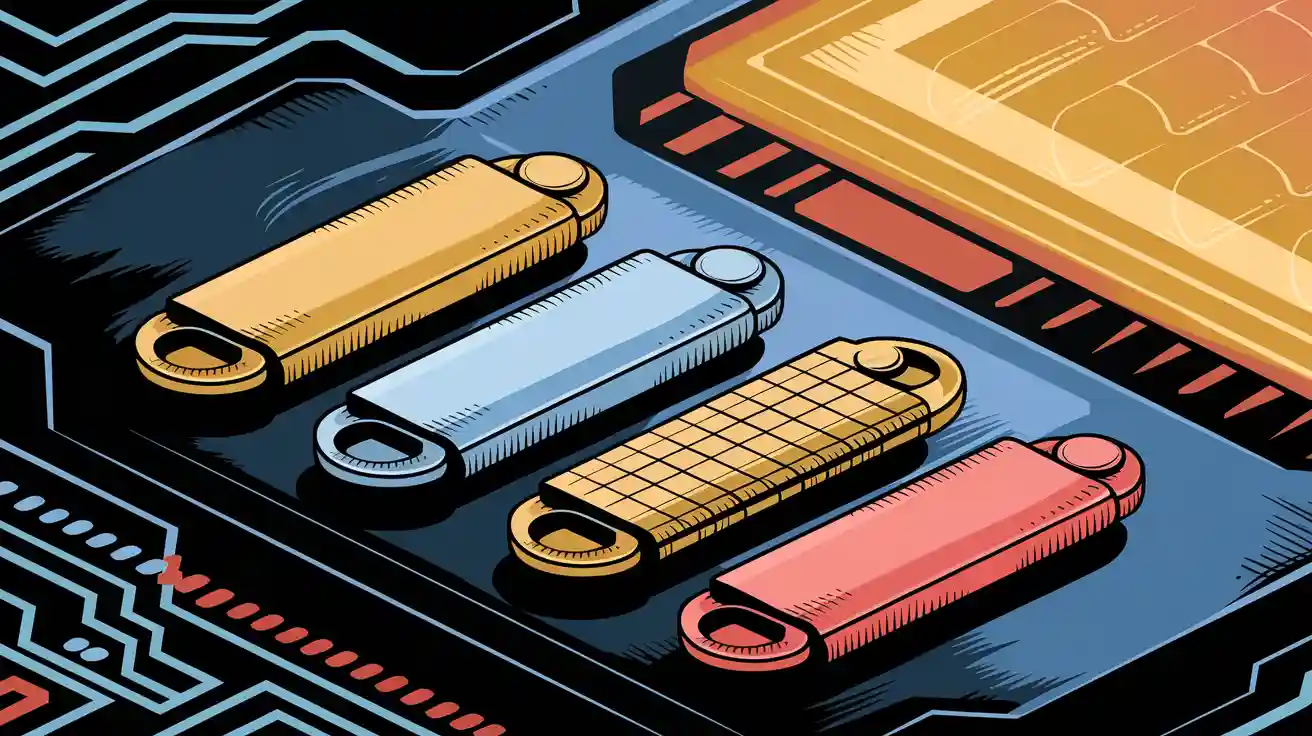
When designing the tab of lipo batteries, selecting the right materials plays a critical role in optimizing battery performance. Copper, aluminum, and nickel stand out as the leading choices. These materials influence the efficiency, durability, and overall functionality of lithium-ion batteries. Their properties directly impact the ion flow, manufacturing process, and the reliability of battery tabs in various applications.
Key Takeaways
Copper is great for battery tabs because it conducts electricity well. This helps energy flow easily with little waste.
Aluminum is light and cheap, so it works well when saving space and weight is important.
Nickel is strong and doesn’t rust easily, making it good for reliable uses.
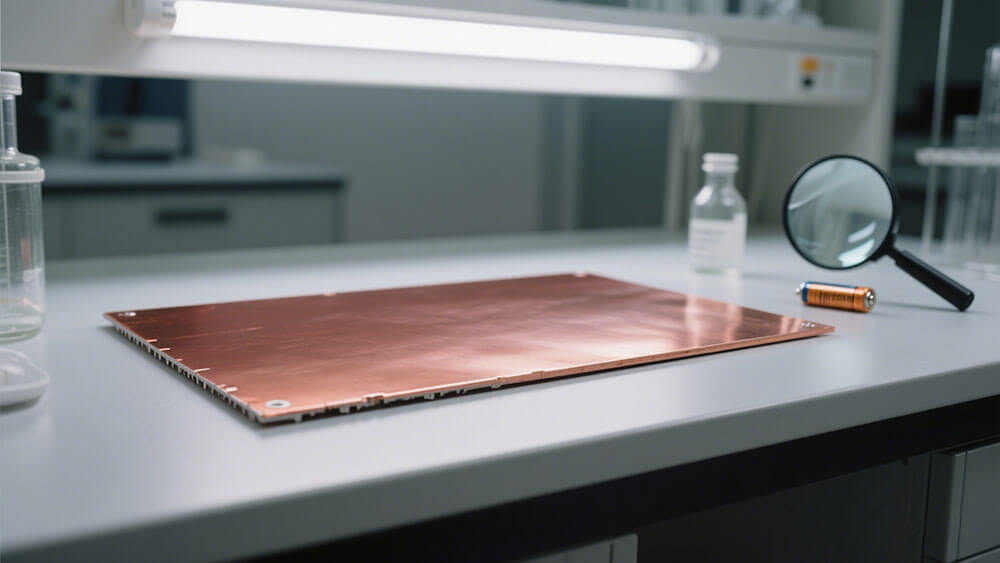
Part 1: Copper for Battery Tabs
1.1 High Conductivity for Efficient Current Flow
Copper stands out as the most conductive material for battery tabs, making it an ideal choice for applications requiring efficient current flow. Its exceptional electrical conductivity, measured at 5.96 × 10⁷ S/m at 20°C, surpasses other materials like nickel, which has a conductivity of only 1.43 × 10⁷ S/m. This high conductivity ensures minimal resistance, allowing ions to move smoothly within the battery, thereby reducing energy loss and improving overall efficiency.
Recent advancements in plating technologies have further enhanced copper’s performance. Nickel-plated copper tabs now offer improved corrosion resistance and durability, making them suitable for long-lasting lithium-ion battery systems. These innovations have made copper indispensable in high-performance applications such as electric vehicles and energy storage systems.
1.2 Durability and Resistance to Mechanical Stress
Copper’s mechanical properties make it highly durable and resistant to stress, which is crucial for the demanding environments of lithium-ion batteries. Its high tensile strength allows it to withstand the mechanical stresses caused by repeated charge and discharge cycles. This durability ensures that the tabs maintain their structural integrity, even under high current loads or in extreme conditions.
Moreover, copper’s ability to resist fatigue and deformation makes it a reliable choice for applications where the battery undergoes frequent mechanical vibrations, such as in robotics or industrial equipment. By choosing copper for the tab of lipo batteries, manufacturers can ensure long-term reliability and safety.
Tip: For applications requiring both high conductivity and durability, nickel-plated copper tabs offer an excellent balance, combining copper’s electrical properties with nickel’s corrosion resistance.
1.3 Applications in High-Performance Lithium-Ion Batteries
Copper is a preferred material for the negative terminal in lithium-ion batteries due to its superior electrical and thermal properties. Its ability to handle high currents makes it indispensable in high-performance applications such as automotive batteries, energy storage systems, and industrial equipment. For instance, in electric vehicles, copper tabs enable efficient energy transfer, supporting rapid charging and discharging processes.
Additionally, copper’s excellent thermal conductivity helps dissipate heat generated during the battery’s operation, reducing the risk of overheating and enhancing safety. This makes it a critical component in applications where thermal management is essential, such as medical devices and consumer electronics.
Key Applications of Copper Tabs:
Automotive batteries for electric vehicles
Energy storage systems for renewable energy
Robotics and industrial equipment
Consumer electronics requiring high energy density
For customized solutions tailored to your specific application, explore our custom battery solutions.
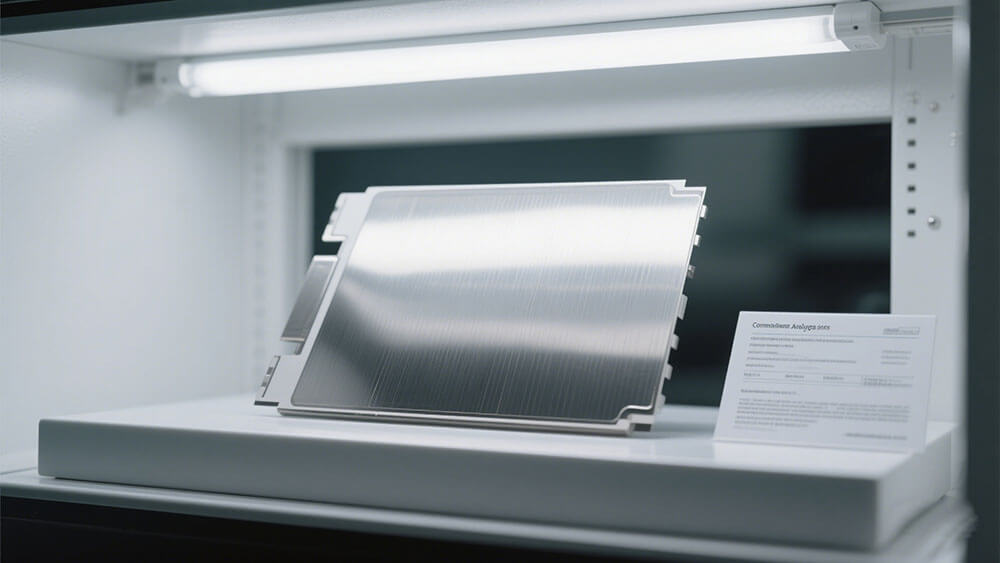
Part 2: Aluminum in the Tab of Lipo Batteries
2.1 Lightweight Design for Enhanced Energy Density
Aluminum’s lightweight nature makes it a standout choice for the tab of lipo batteries, especially in applications where energy density is a priority. With a density of just 2.7 g/cm³, aluminum significantly reduces the overall weight of the battery. This characteristic is particularly advantageous in portable devices and electric vehicles, where minimizing weight directly translates to improved performance and efficiency.
Key benefits of aluminum’s lightweight design:
Enhances energy density by reducing the weight of the battery cell.
Supports high-performance energy storage solutions.
Facilitates the development of compact and portable battery systems.
Recent advancements in aluminum-ion batteries (AIBs) have further highlighted aluminum’s role in energy density optimization. Innovations such as combining Nb2CTx and MoS2 in cathodes have improved electrochemical kinetics. These advancements enable rapid charge-discharge rates and high stability, which are critical for energy-dense applications. By leveraging aluminum’s properties, you can achieve a balance between performance and weight, making it an ideal material for modern lithium-ion battery designs.
Note: For applications requiring lightweight and energy-efficient solutions, aluminum tabs are an excellent choice.
2.2 Cost-Effectiveness for Large-Scale Production
Aluminum’s affordability makes it a practical option for large-scale battery cell production. Its abundance and relatively low extraction costs contribute to its cost-effectiveness, making it a preferred material for manufacturers aiming to optimize production budgets without compromising quality.
The production process for aluminum tabs is also streamlined, further reducing manufacturing expenses. Unlike other materials, aluminum requires less complex processing, which translates to faster production cycles and lower operational costs. This efficiency is particularly beneficial for industries producing batteries in high volumes, such as consumer electronics and electric vehicles.
Advantages of aluminum in production:
Lower material costs compared to copper or nickel.
Simplified manufacturing processes reduce production time.
Ideal for cost-sensitive applications like portable electronics and renewable energy storage.
By choosing aluminum for the positive electrode tabs, you can achieve a balance between performance and cost, ensuring that your production process remains both efficient and economical.
2.3 Compatibility with Cathode Materials in Lithium-Ion Cells
Aluminum’s compatibility with cathode materials in lithium-ion cells is another reason for its widespread use. It is primarily used for the positive electrode tabs due to its ability to form a stable connection with cathode materials. This compatibility ensures efficient ion flow and minimizes resistance, which is crucial for maintaining the battery’s performance over time.
Studies have shown that aluminum doping in Ni-rich LiNi0.8Co0.2−yAlyO2 cathodes enhances stability and performance. Aluminum oxide coatings form a thicker solid electrolyte interphase (CEI) layer, which inhibits cathode degradation and dissolution. This interaction not only improves the longevity of lithium-ion cells but also enhances their safety, making aluminum an indispensable material in battery design.
Tip: For applications requiring long-lasting and reliable batteries, aluminum tabs provide the necessary stability and compatibility with cathode materials.
By integrating aluminum into your battery design, you can ensure optimal performance, durability, and safety, particularly in high-demand applications like industrial equipment and renewable energy systems.
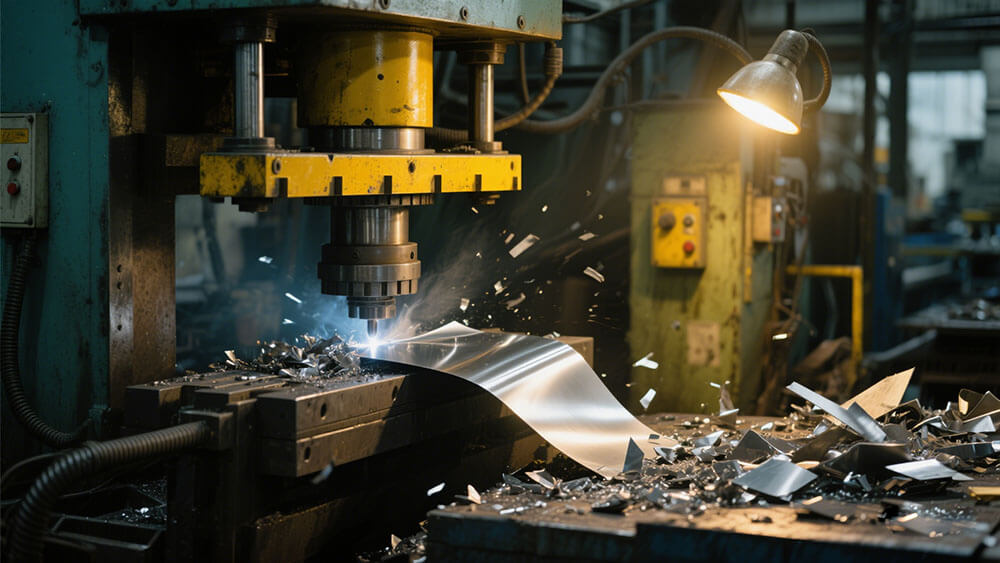
Part 3: Nickel as a Material for Battery Tabs
3.1 Superior Corrosion Resistance for Longevity
Nickel offers exceptional corrosion resistance, making it a reliable choice for the tab of lipo batteries. Its natural ability to withstand harsh chemical environments ensures long-lasting performance, even in demanding conditions. This property is particularly valuable in lithium-ion cells, where exposure to electrolytes can degrade less resistant materials over time.
Key benefits of nickel’s corrosion resistance:
Prolongs the lifespan of battery connections.
Maintains stable performance in high-humidity or chemically aggressive environments.
Reduces maintenance needs, enhancing the overall reliability of the battery system.
By incorporating nickel into your battery design, you can achieve enhanced durability and longevity, especially in applications requiring consistent performance under challenging conditions.
3.2 High Mechanical Strength for Reliable Performance
Nickel’s mechanical strength ensures that battery tabs remain structurally sound during production and operation. Its ability to withstand mechanical stress makes it ideal for applications where batteries face frequent vibrations or physical impacts.
Property | Annealed | Cold Rolled |
---|---|---|
Ultimate Tensile Strength | 55,000 PSI | 105,000 PSI |
Yield Strength (0.2% Offset) | 15,000 PSI | 100,000 PSI |
Elongation in 2” | 40% | 20% |
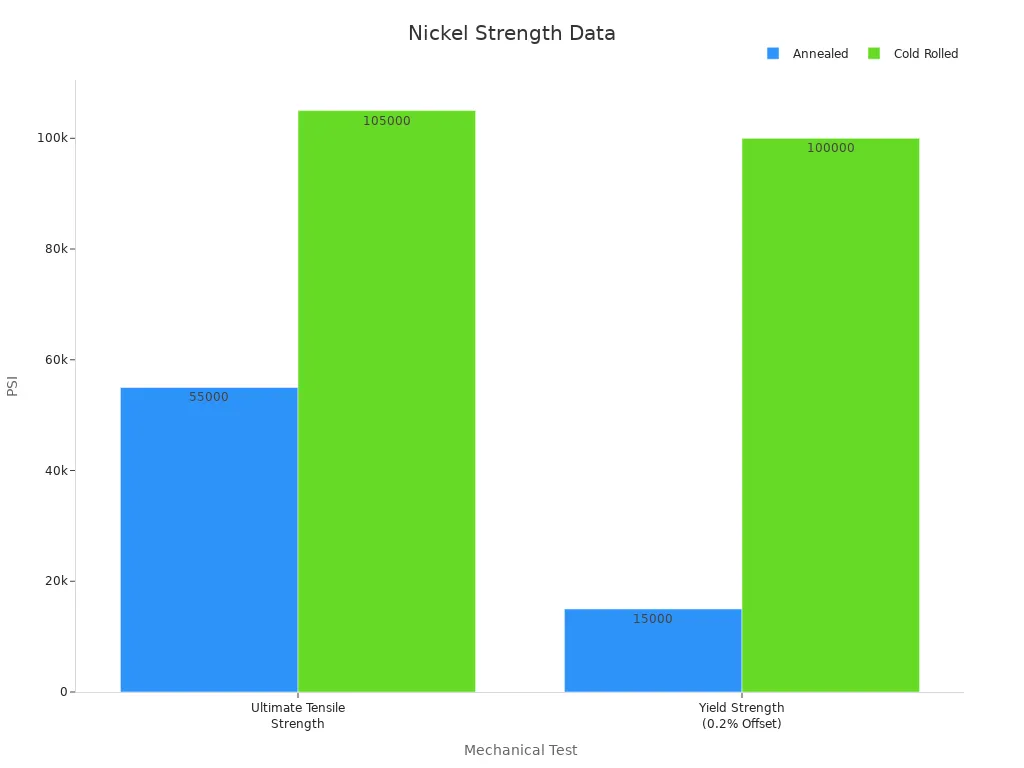
This combination of tensile strength and elongation ensures that nickel tabs can endure the rigors of battery cell production without compromising their integrity. For manufacturers, this translates to fewer defects and higher reliability in the final product.
3.3 Role in Specialized and High-Reliability Applications
Nickel plays a crucial role in specialized applications where reliability is paramount. Its superior corrosion resistance and mechanical strength make it indispensable in industries like robotics, medical devices, and industrial equipment. For example, nickel tabs are often used in batteries for robotics, where consistent performance under mechanical stress is essential. Explore robotics battery solutions.
In medical applications, nickel’s stability ensures safe and reliable energy delivery, which is critical for life-saving devices. Learn more about medical battery solutions. Additionally, nickel’s compatibility with the negative electrode in lithium-ion cells enhances its role in high-reliability systems, such as security systems and infrastructure projects.
By choosing nickel for your battery tabs, you can ensure optimal performance in applications where durability, safety, and reliability are non-negotiable. For tailored solutions, consider consulting Large Power’s custom battery solutions.
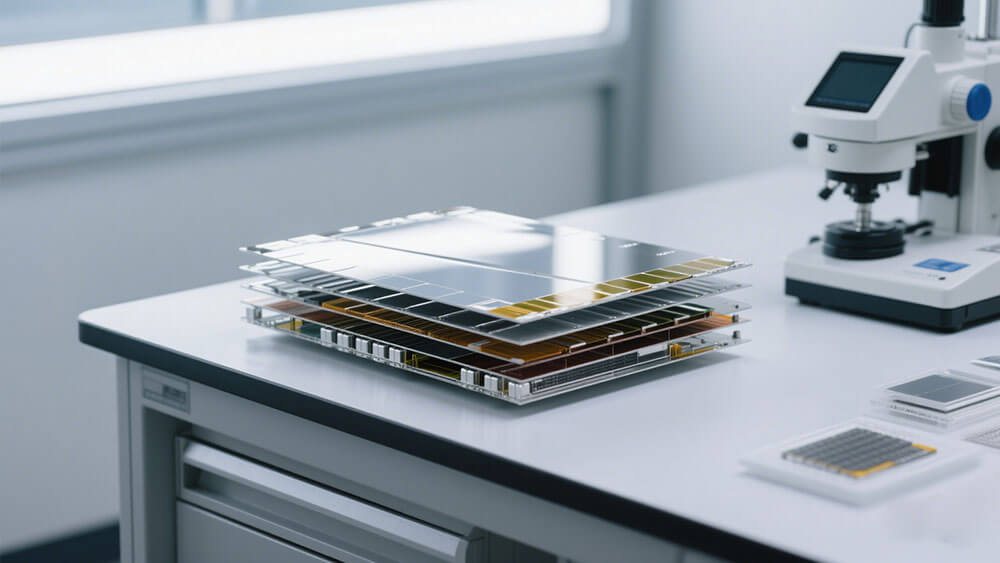
Part 4: Comparison of Materials for Battery Tabs
4.1 Conductivity and Electrical Performance
When comparing conductivity, copper outshines both aluminum and nickel. Its resistivity of 1.68 × 10⁻⁸ Ω·m at 20°C translates to a conductivity of 5.96 × 10⁷ S/m, making it approximately 4.17 times more conductive than nickel. This superior conductivity ensures minimal energy loss, which is critical for high-performance lithium-ion batteries. Nickel, while offering excellent corrosion resistance, has a higher resistivity of 6.99 × 10⁻⁸ Ω·m, leading to greater energy dissipation as heat.
Material | Resistivity (Ω·m) at 20°C | Conductivity (S/m) at 20°C |
---|---|---|
Copper | 1.68 × 10⁻⁸ | 5.96 × 10⁷ |
Nickel | 6.99 × 10⁻⁸ | 1.43 × 10⁷ |
Copper’s high electron mobility and longer mean free path contribute to its exceptional conductivity. Aluminum, while less conductive than copper, offers a balance between performance and weight, making it suitable for applications prioritizing energy density.
Tip: For applications requiring high current flow, copper tabs are the optimal choice due to their unmatched conductivity.
4.2 Cost and Manufacturing Feasibility
Aluminum stands out as the most cost-effective material for battery tab production. Its abundance and straightforward processing methods reduce manufacturing expenses, making it ideal for large-scale production. Copper, while more expensive, justifies its cost with superior conductivity and durability. Nickel, often used in specialized applications, incurs higher costs due to its excellent corrosion resistance and mechanical strength.
For manufacturers, balancing cost with performance is crucial. Aluminum offers affordability, while copper and nickel cater to high-performance and reliability-focused applications.
4.3 Durability and Corrosion Resistance
Nickel excels in corrosion resistance, making it a reliable choice for long-lasting battery tabs. It withstands harsh chemical environments, ensuring stable performance over time. Copper, although highly conductive, requires protective coatings to prevent corrosion. Aluminum offers moderate corrosion resistance but may degrade faster in aggressive environments.
Material Type | Conductivity | Corrosion Resistance | Notes |
---|---|---|---|
Nickel | High | Excellent | Commonly used in lithium-ion batteries. |
Aluminum | Moderate | Good | Lightweight but lower conductivity. |
Copper | Very High | Prone to corrosion | Requires protective coatings. |
The choice of material depends on the application. For environments with high humidity or chemical exposure, nickel provides unmatched reliability.
4.4 Weight and Impact on Energy Density
Aluminum’s lightweight nature significantly enhances energy density. With a density of 2.7 g/cm³, it reduces the overall weight of the battery, making it ideal for portable devices and electric vehicles. Copper, while heavier, offers superior conductivity, which is crucial for high-performance applications. Nickel, with a density similar to copper, is often reserved for specialized uses where weight is less critical.
Note: Researchers have highlighted that solid-state lithium metal batteries achieve higher energy density at lower weights, showcasing the importance of material selection in battery design.
By understanding the trade-offs between weight and performance, you can select the right material to optimize your battery’s energy density and efficiency.
Copper, aluminum, and nickel each bring unique strengths to the tab of lipo batteries, making them indispensable in lithium-ion battery designs. Copper excels in conductivity and durability, ensuring efficient energy transfer and long-term reliability. Aluminum offers a lightweight and cost-effective solution, ideal for applications prioritizing energy density. Nickel provides unmatched corrosion resistance and mechanical strength, making it suitable for high-reliability environments.
Energy density regulations, such as the European Battery Partnership’s 2030 target of 500 Wh/kg, continue to drive innovation in tab materials, emphasizing the need for lightweight and efficient designs.
Manufacturers should evaluate their specific requirements, including cost, energy density, and application environment, to select the most suitable material. Raw material price volatility, influenced by geopolitical tensions and supply chain disruptions, further highlights the importance of dynamic cost management in the selection process. For tailored solutions, explore Large Power’s custom battery solutions.
FAQ
1. What is the primary role of battery tabs in lithium-ion batteries?
Battery tabs connect the electrodes to the external circuit, enabling efficient current flow. They ensure optimal performance and safety in lithium-ion batteries.
2. Why is copper commonly used for negative tabs in LiPo batteries?
Copper offers superior conductivity and durability, making it ideal for high-performance lithium-polymer batteries in demanding applications like robotics and industrial systems.
3. How does material selection impact battery performance?
The choice of tab material affects conductivity, weight, and corrosion resistance. For tailored solutions, consult Large Power for expert guidance.