Contents
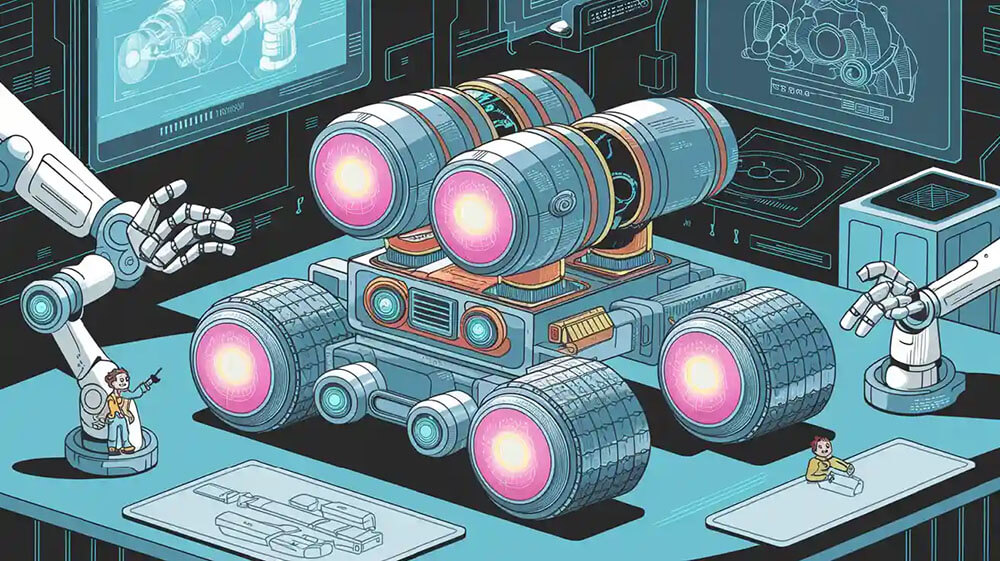
Cell to Chassis (CTC) for Robots is transforming the robotics industry by integrating battery cells directly into the robot’s chassis. This innovative approach removes the need for separate battery packs, leading to reduced weight and a more streamlined design. According to Euan McTurk, a battery electrochemist, this method turns the cell casing into a structural element, boosting both efficiency and cost-effectiveness. The implementation of CTC for Robots aligns with broader energy transition trends, as seen with CTP-equipped vehicles making up 48.6% of new energy vehicle sales in 2023. By applying CTC technology to robotics, the industry is set to achieve groundbreaking advancements, enabling the creation of more efficient and powerful robotic systems.
Key Takeaways
Cell to Chassis (CTC) technology combines battery cells with the robot’s frame. This makes robots lighter and saves space for better use.
CTC technology improves energy use. Robots can work longer and do more tasks in areas like factories or hospitals.
Using CTC technology can save money when making robots. It uses fewer materials and makes building robots easier.
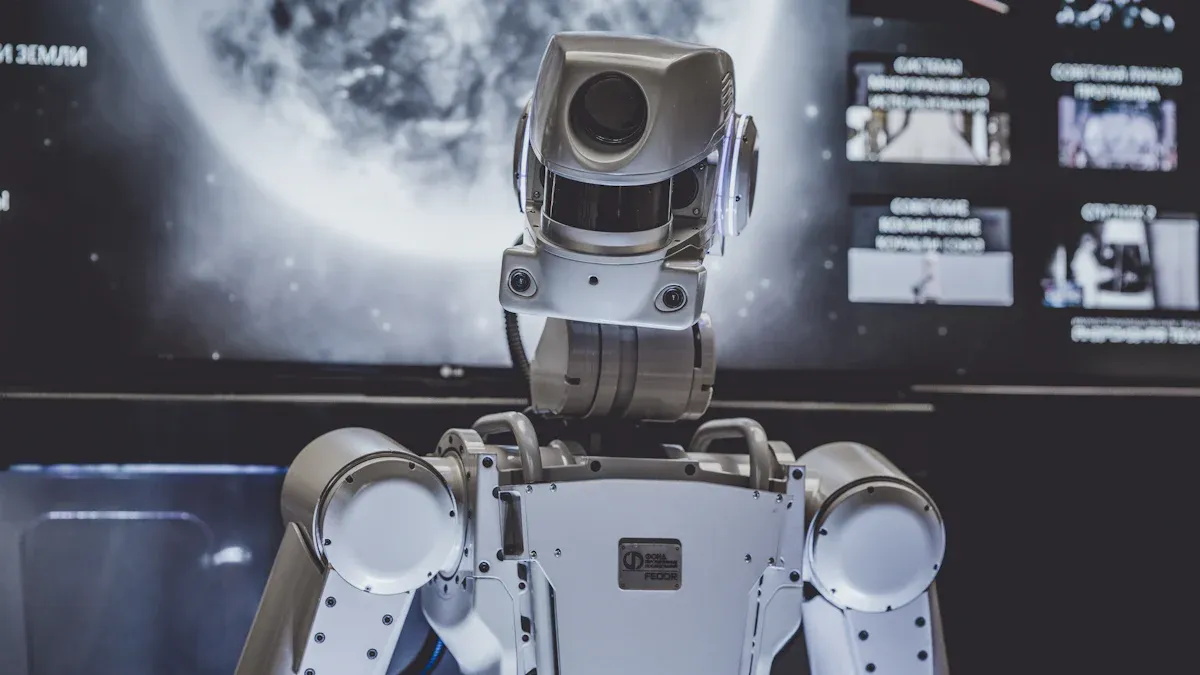
Part 1: Understanding Cell to Chassis (CTC) for Robots
1.1 What is CTC Technology?
Cell to Chassis (CTC) technology represents a groundbreaking approach in robotics and energy systems. It eliminates the traditional battery pack by integrating battery cells directly into the chassis structure. This design not only reduces weight but also optimizes space, enabling more compact and efficient robotic systems. By removing intermediary layers, CTC technology enhances energy density and structural integrity, making it a preferred choice for next-generation robotics.
The concept of CTC technology has its roots in the electric vehicle (EV) industry, where it has been extensively researched and implemented. Reports like “Materials for Electric Vehicle Battery Cells and Packs 2025-2035” highlight its transformative potential. The integration of battery cells into the chassis demands advanced materials and precise engineering, ensuring both performance and safety. As robotics continues to evolve, adopting this technology will drive significant advancements in design and functionality.
1.2 How Does CTC Technology Work in Robotics?
CTC technology in robotics involves embedding battery cells directly into the robot’s structural framework. Instead of housing batteries in separate compartments, the cells become an integral part of the chassis. This integration requires meticulous planning to ensure that the battery cells contribute to the robot’s structural strength without compromising safety or performance.
For example, in a robot designed for industrial applications, the chassis must withstand heavy loads and rigorous operations. By using CTC technology, you can achieve a lighter yet sturdier design. The battery cells, often made from advanced lithium-ion chemistries like NMC or LiFePO4, are strategically placed to distribute weight evenly. This not only improves the robot’s balance but also enhances its energy efficiency.
Thermal management is another critical aspect of CTC technology. Since the battery cells are embedded within the chassis, effective cooling mechanisms are essential to prevent overheating. Advanced materials and cooling systems are employed to maintain optimal operating temperatures, ensuring the robot’s reliability and longevity.
1.3 Core Principles of Cell-to-Body Technology
Cell-to-body technology, a broader concept encompassing CTC, revolves around three core principles: integration, efficiency, and sustainability. These principles guide the design and implementation of CTC technology in robotics.
Integration: The seamless incorporation of battery cells into the robot’s chassis eliminates the need for separate battery enclosures. This integration reduces material usage and simplifies the manufacturing process, resulting in cost savings and a more streamlined design.
Efficiency: By embedding the battery cells directly into the chassis, you can achieve higher energy density and better weight distribution. This leads to improved performance, longer operational times, and reduced energy consumption.
Sustainability: CTC technology aligns with global energy transition goals by promoting the use of efficient and eco-friendly energy systems. The reduced material usage and enhanced energy efficiency contribute to a lower carbon footprint, making it a sustainable choice for robotics and other industries.
As you explore the potential of cell-to-body technology, it’s essential to consider its implications for safety and performance. The integration of battery cells into the chassis demands rigorous testing and quality control to ensure that the robots meet industry standards. By adhering to these principles, you can harness the full potential of CTC technology to create innovative and sustainable robotic solutions.
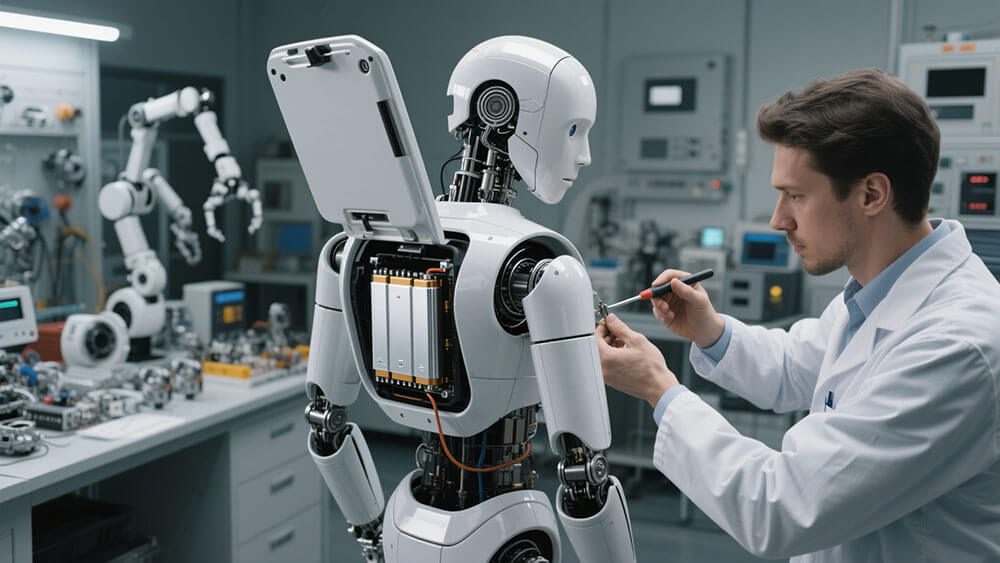
Part 2: Benefits of CTC Technology in Robotics
2.1 Weight Reduction and Space Optimization
Cell to Chassis (CTC) technology revolutionizes robotic design by significantly reducing weight and optimizing space. By integrating battery cells directly into the chassis, you eliminate the need for bulky battery enclosures. This streamlined approach not only minimizes material usage but also frees up valuable internal space for additional components or payloads.
The weight reduction enhances the mobility and agility of robots, especially in industrial applications where efficiency is critical. A lighter chassis also reduces energy consumption, allowing robots to operate for longer periods without compromising performance.
By adopting cell-to-body technology, you can achieve a balance between structural integrity and compact design. This optimization is particularly beneficial for robots used in confined environments, such as medical facilities or infrastructure maintenance.
Tip: If you’re exploring custom battery solutions for robotics, consider consulting experts to maximize the benefits of CTC technology.
2.2 Enhanced Energy Efficiency and Performance
CTC technology improves energy efficiency by embedding battery cells directly into the robot’s structural framework. This integration reduces energy losses associated with traditional battery pack designs. With better weight distribution and higher energy density, robots can achieve superior performance and longer operational times.
For example, lithium-ion batteries, such as NMC or LiFePO4, are commonly used in CTC systems due to their high energy density and durability. NMC batteries offer an energy density of 160–270 Wh/kg, while LiFePO4 batteries provide 100–180 Wh/kg with exceptional cycle life. These characteristics make them ideal for robots requiring consistent power output over extended periods.
Thermal management also plays a crucial role in maintaining performance. Advanced cooling systems integrated into the chassis ensure that battery cells operate within optimal temperature ranges, preventing overheating and extending battery life. This feature is particularly important for robots used in high-demand environments, such as industrial or security applications.
By leveraging CTC technology, you can enhance the reliability and efficiency of robotic systems, aligning with global energy transition goals. This approach not only reduces energy consumption but also supports sustainable practices in robotics.
2.3 Cost-Effectiveness in Robotic Manufacturing
CTC technology offers significant cost advantages in robotic manufacturing. By eliminating the need for separate battery enclosures and reducing material usage, you can lower production costs while maintaining high-quality standards.
By applying similar methodologies to CTC technology, you can achieve cost savings at scale. The iterative design process ensures that systems meet market demands while optimizing production efficiency.
Additionally, the reduced material usage aligns with sustainability goals, further enhancing the value proposition of CTC technology. For businesses seeking to adopt eco-friendly practices, this approach offers a competitive edge in the robotics industry.
Note: To explore how CTC technology can reduce manufacturing costs for your robotic systems, visit Large Power’s custom battery solutions.
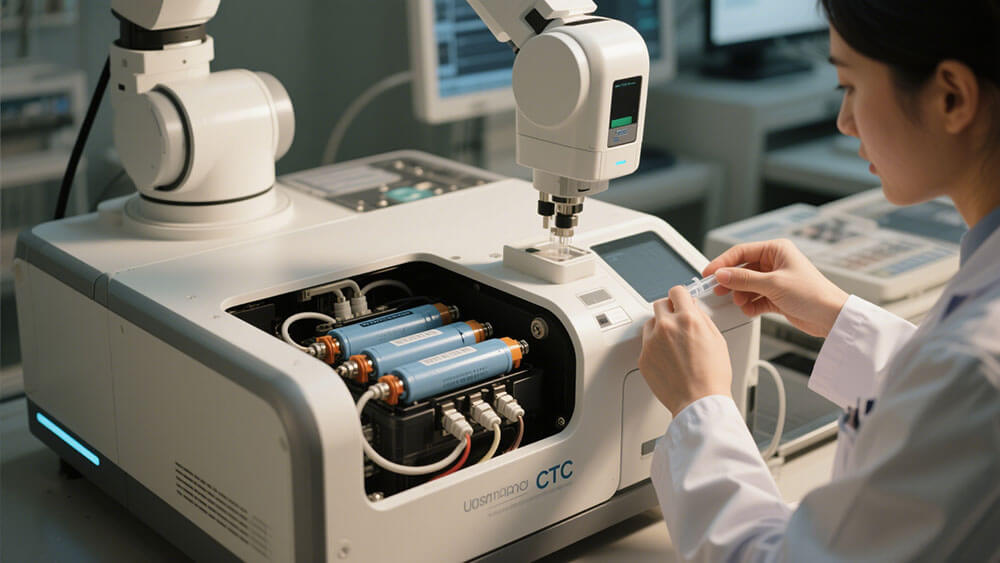
Part 3: Safety and Performance Considerations
3.1 Structural Integrity of CTC-Integrated Robots
The structural integrity of robots utilizing cell-to-chassis technology is a critical consideration. By embedding battery cells directly into the chassis, you create a design where the battery serves as both an energy source and a structural component. This dual functionality demands advanced engineering to ensure the robot can withstand operational stresses without compromising safety.
For example, industrial robots often operate in environments with heavy loads and vibrations. The chassis must maintain its rigidity while protecting the embedded battery cells. Engineers achieve this by using high-strength materials like aluminum alloys or carbon composites. These materials provide durability while keeping the overall weight low, enhancing the robot’s performance.
Testing plays a vital role in ensuring structural integrity. Simulations and real-world stress tests help identify potential weak points in the design. By addressing these issues early, you can ensure that the robot meets industry standards for safety and reliability.
3.2 Reliability and Durability in Robotic Operations
Reliability is essential for robots in demanding applications. CTC technology enhances durability by reducing the number of components, which minimizes potential failure points. The integrated battery pack design also simplifies maintenance, as fewer parts require inspection or replacement.
For instance, robots used in security systems must operate continuously without interruptions. The robust design of CTC-integrated robots ensures consistent performance even under challenging conditions. Lithium-ion batteries, such as NMC or LiFePO4, are commonly used due to their high cycle life and energy density. NMC batteries, for example, offer a cycle life of 1,000–2,000 cycles, making them ideal for long-term use.
Regular maintenance protocols further enhance reliability. Monitoring systems can track battery health and performance, allowing you to address issues proactively. This approach reduces downtime and extends the robot’s operational lifespan.
3.3 Thermal Management and Safety Protocols
Thermal management is a crucial aspect of CTC technology. Embedded battery cells generate heat during operation, which can affect performance and safety. Effective cooling systems are essential to maintain optimal temperatures and prevent overheating.
Engineers use advanced cooling techniques, such as liquid cooling or heat sinks, to dissipate heat efficiently. These systems ensure that the battery cells remain within safe temperature ranges, even during high-demand operations. For example, robots used in industrial environments often face intense workloads. Proper thermal management prevents thermal runaway, a condition where excessive heat leads to battery failure.
Safety protocols also play a significant role. Sensors can monitor temperature, voltage, and current in real-time, providing early warnings of potential issues. By integrating these safety measures, you can ensure the reliability and safety of CTC-equipped robots in various applications.
Tip: To explore custom battery solutions with advanced safety features, visit Large Power’s custom battery solutions.
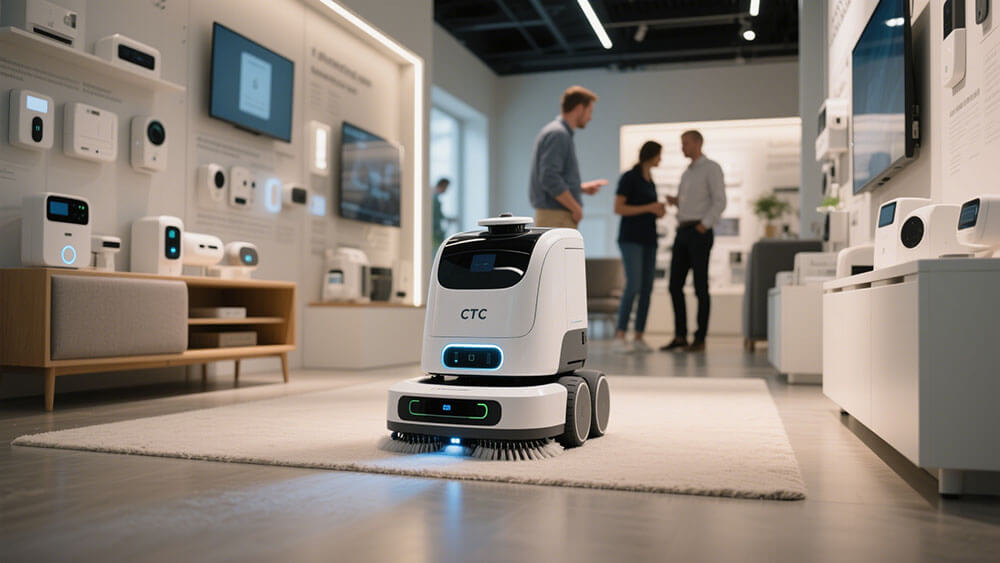
Part 4: Future Potential of CTC Technology in Robotics
4.1 Innovations in Battery Integration for Robotics
The future of robotics will see groundbreaking advancements in battery integration. Solid-state batteries are emerging as a game-changer, offering improved safety and higher energy density. These batteries reduce the risk of overheating, making them ideal for robots operating in demanding environments. Wireless charging is another innovation transforming the industry. It allows robots to recharge efficiently without manual intervention, enhancing operational convenience.
Advanced battery management systems (BMS) are also gaining traction. These systems optimize battery performance by monitoring energy usage and extending battery life. Customized battery packs tailored to specific robotic applications are becoming more common. This trend ensures that robots achieve peak performance while meeting unique operational requirements. Additionally, the growing interest in sustainable and eco-friendly battery solutions aligns with global energy transition goals, paving the way for greener robotics.
4.2 Expanding Applications Across Robotic Industries
CTC technology is unlocking new possibilities across various robotic industries. In healthcare, robots equipped with CTC systems can operate longer, enabling uninterrupted patient care. Industrial robots benefit from enhanced energy efficiency, allowing them to handle heavy workloads with reduced downtime. The logistics sector is also leveraging CTC technology to improve the performance of autonomous delivery robots.
The first EV with CTC technology demonstrated the potential of this innovation, inspiring its adoption in robotics. As electric vehicles revolutionize transportation, similar advancements are reshaping robotics. The integration of CTC technology ensures that robots remain agile and efficient, even in high-demand applications. This versatility makes it a valuable asset across diverse industries.
4.3 Long-Term Impacts on Robotic Design and Functionality
The adoption of CTC technology will redefine robotic design and functionality. By embedding battery cells directly into the chassis, you can create robots with lighter and more compact designs. This approach enhances mobility and allows robots to navigate confined spaces with ease. The improved weight distribution also boosts energy efficiency, enabling longer operational times.
The influence of electric car innovations on robotics is undeniable. As EV technologies evolve, they inspire similar advancements in robotic systems. The shift toward integrated designs reduces manufacturing complexity and costs, making robotics more accessible. Over time, CTC technology will drive the development of smarter, more sustainable robots, shaping the future of automation.
Cell to Chassis (CTC) technology redefines robotics by integrating battery cells directly into the chassis, enhancing energy efficiency, reducing weight, and optimizing space. Its transformative impact spans industrial, medical, and security applications. Future advancements, like solid-state batteries, promise even greater innovation.
FAQ
1. How does Cell to Chassis technology improve robotic efficiency?
CTC technology reduces weight and optimizes space, enabling robots to operate longer, move faster, and handle tasks with greater precision.
2. Is CTC technology safe for industrial robots?
Yes, engineers use advanced materials and cooling systems to ensure structural integrity and prevent overheating during demanding operations.
3. Can CTC technology be applied to all types of robots?
CTC technology suits most robots, especially those requiring compact designs, high energy efficiency, and durability in challenging environments.
Explore custom solutions with Large Power.