Contents
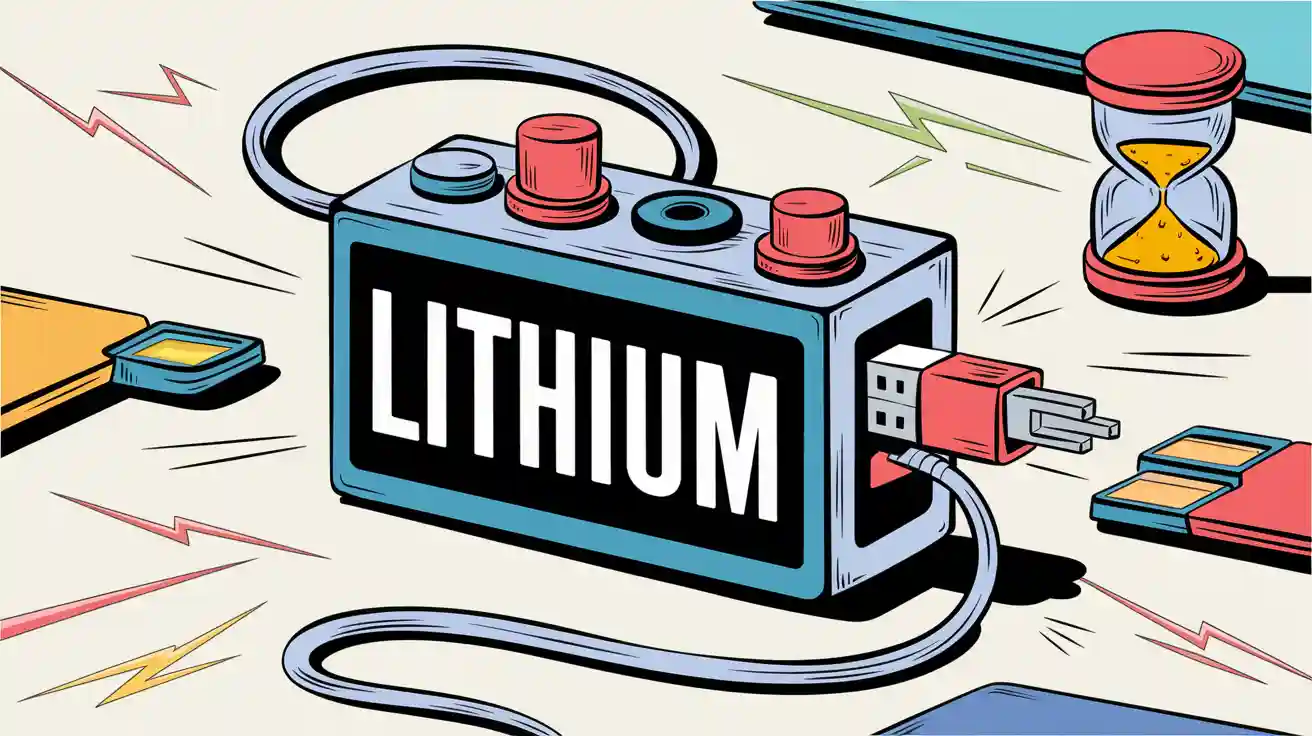
Improving the charging speed of lithium battery systems presents several challenges, such as internal resistance, temperature sensitivity, material constraints, and state of charge effects. These limitations arise from the distinct properties of lithium-ion batteries. Effectively managing these factors is crucial to achieving optimal charging speed of lithium battery performance, safety, and durability, particularly in rigorous industrial applications.
Key Takeaways
Internal resistance slows charging. Control it for better battery safety.
Heat changes lithium-ion movement. Watch it to charge faster and stay safe.
Use better materials for parts. This helps batteries charge quicker and last longer.
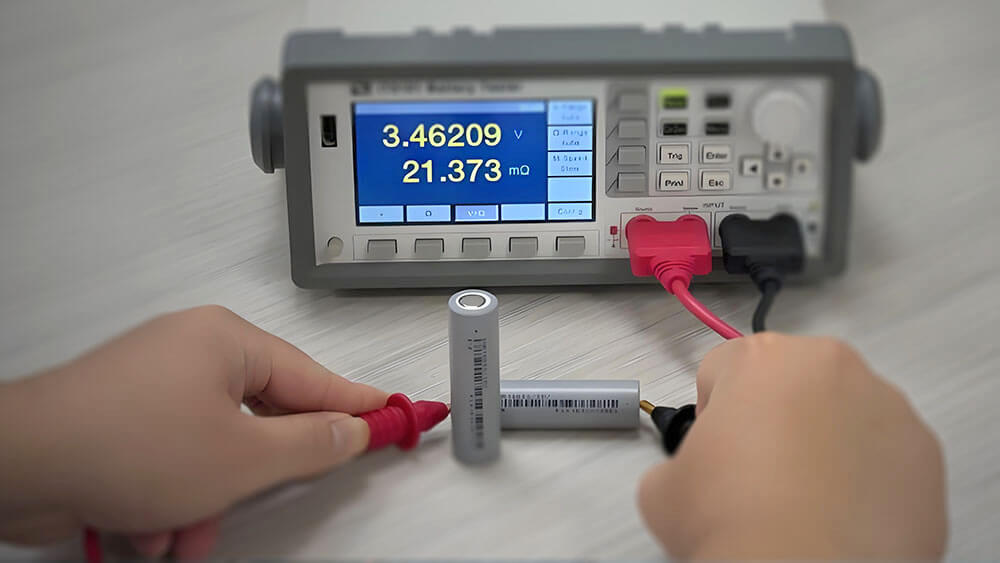
Part 1: Internal Resistance and Current
1.1 How internal resistance limits the charging speed of lithium battery
Internal resistance plays a critical role in determining the charging speed of a lithium battery. When you charge a battery, the internal resistance opposes the flow of current, causing energy loss in the form of heat. This resistance increases as the battery ages or when it operates under extreme conditions, such as high temperatures or low states of charge (SOC). As a result, the maximum charging rate is directly influenced by the battery’s internal resistance.
To better understand this relationship, consider the following data:
Measurement Time (seconds) | Resistance (mΩ) | |
---|---|---|
0.1 | Similar | All |
2 | 0.73 (1C) | 1C |
5 | 0.39 (15C) | 15C |
10 | Varies | Higher currents |
This table highlights how resistance and current interact over time. At higher charge-discharge rates, the resistance decreases initially but stabilizes as the battery approaches its thermal limits. This phenomenon underscores the importance of managing internal resistance to optimize the charging speed of lithium batteries.
1.2 Heat generation due to high current
High-current charging is a double-edged sword. While it enables faster charging, it also generates significant heat due to the internal resistance of the battery. This heat can lead to thermal runaway, a dangerous condition where the battery’s temperature rises uncontrollably. Overheating not only reduces the battery’s lifespan but also poses serious safety risks.
Fast charging technology must address this challenge by balancing the charge and discharge rate. For instance, increased voltage charging can accelerate the process, but it also amplifies heat generation. Advanced thermal management systems and materials with better heat dissipation properties are essential to mitigate these risks.
1.3 Balancing current for safety and efficiency
Achieving a balance between safety and efficiency is crucial for high-current charging. You must consider several factors, including the SOC, peripheral charging equipment, and the battery’s chemistry. Here are some key points to keep in mind:
Higher SOC increases internal resistance, slowing the charging speed.
Fast charging can trigger abnormal reactions, such as lithium plating, which raises internal resistance and temperature.
Peripheral charging equipment, such as chargers and connectors, may limit the maximum charge rate.
By carefully managing these variables, you can enhance the performance and longevity of lithium batteries. For industrial applications, adopting customized battery solutions tailored to specific requirements can further optimize safety and efficiency. You can explore such solutions from Large Power.
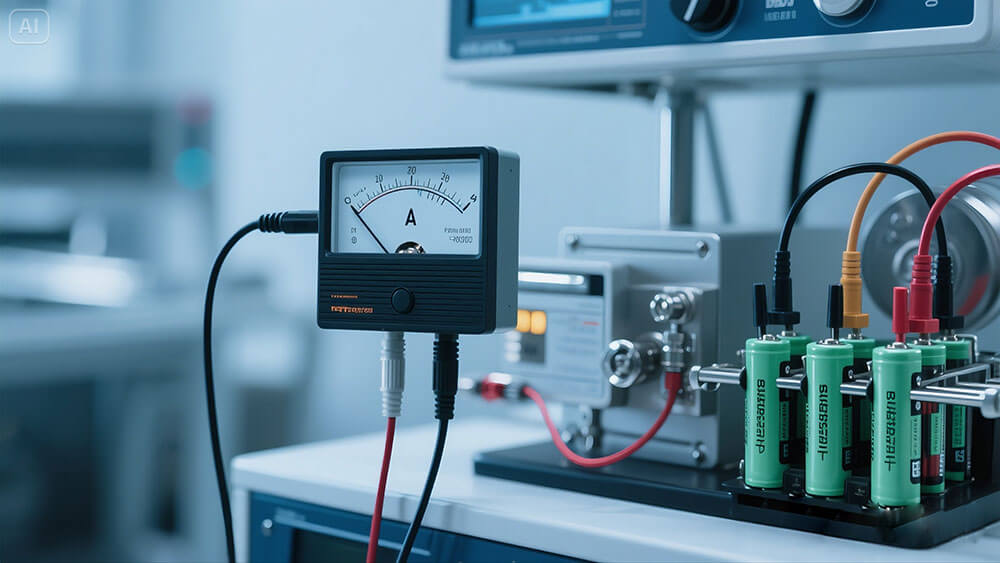
Part 2: Temperature Effects on Lithium Ion Battery
2.1 The role of temperature in lithium-ion diffusion
Temperature significantly influences the diffusion process in lithium-ion batteries. At lower temperatures, the transport of lithium ions (Li+) through the electrolyte and the solid electrolyte interphase (SEI) layer slows down. This creates a kinetic bottleneck, increasing resistance and reducing the battery’s overall efficiency. Conversely, higher temperatures enhance the migration velocity of solvated Li+, improving mass transfer and ionic conductivity. However, excessive heat can degrade the microstructure of the battery, impacting its long-term performance.
Evidence Description | Key Findings |
---|---|
Effect of Temperature on Li+ Transport | Lower temperatures slow Li+ transport, leading to incomplete electrolyte decomposition. |
Kinetic Bottleneck | Low temperatures hinder Li+ diffusion through the SEI layer, increasing resistance. |
Migration Velocity | Temperature affects the migration velocity of solvated Li+, influencing conductivity. |
Microstructure Influence | Understanding temperature’s impact on microstructure is crucial for performance. |
For industrial applications, you must carefully monitor temperature to optimize lithium-ion battery performance. Advanced thermal management systems can help mitigate the negative effects of extreme temperatures.
2.2 Overheating risks during fast charging
Fast charging generates significant heat, which can lead to overheating. High-current charging stresses battery materials, accelerating degradation and reducing capacity. Increased voltage charging, while speeding up the process, raises the risk of over-voltage damage. Excessive heat can also cause lithium plating on the anode, a condition that compromises safety and shortens the battery’s lifespan.
High-current charging generates more heat, stressing battery materials.
Increased heat degrades the electrolyte and reduces capacity.
Lithium plating during fast charging poses safety risks and leads to capacity loss.
To address these risks, you should implement robust thermal management systems and avoid pushing the battery beyond its thermal limits. For customized solutions tailored to your needs, consider consulting experts in the field. Learn more from Large Power.
2.3 Cold temperatures and their impact on charging speed
Cold temperatures present unique challenges for lithium-ion batteries. As the temperature drops, the internal resistance of the battery increases, slowing down the charging process. Consumer-grade lithium-ion batteries cannot be charged below 0°C (32°F) due to the risk of lithium plating, which causes permanent performance degradation. Advanced chargers often prevent charging below freezing to protect the battery.
Extreme cold increases internal resistance, reducing power output.
Charging below freezing risks lithium plating, leading to safety concerns.
Industrial-grade chargers include safeguards to prevent charging in sub-zero conditions.
For industrial applications, you should consider battery systems designed to operate in extreme environments. These systems ensure reliable performance and safety, even under challenging conditions. Explore more about industrial battery solutions from Large Power.
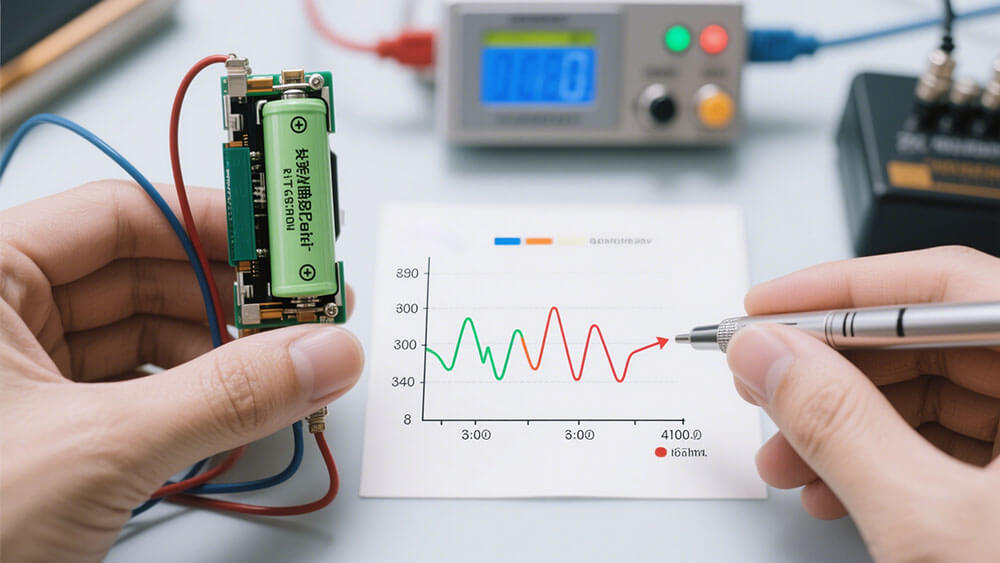
Part 3: Material Properties and the Impact of Fast Charging
3.1 Electrode materials and their influence on charging speed
Electrode materials play a pivotal role in determining how quickly a lithium-ion battery can charge. Graphite anodes, commonly used in lithium-ion batteries, exhibit limitations during fast charging due to side reactions like lithium plating and solid electrolyte interface (SEI) film growth. These reactions hinder the battery’s performance and longevity. A study using a P2D model revealed that lithium plating significantly contributes to capacity loss during the early stages of charging, while SEI film growth becomes more prominent later. This highlights the need for advanced electrode materials that can minimize these effects and support faster charging without compromising safety or durability.
For industrial applications, selecting the right electrode material is critical. Materials like silicon-doped anodes or lithium-titanate (LTO) offer promising alternatives due to their higher charge acceptance and reduced risk of degradation. However, these materials often come with trade-offs, such as lower energy density, which must be balanced based on the specific use case.
3.2 Electrolyte limitations in high-speed charging
The electrolyte serves as the medium for lithium-ion transport, and its properties directly affect the impact of fast charging. Studies have shown that solution-phase diffusion limitations, particularly in thicker electrodes or low salt concentrations, are a major bottleneck during high-speed charging. For example:
Study | Findings |
---|---|
Doyle et al. | Identified significant solution-phase diffusion limitations in thicker electrodes. |
Arora et al. | Found that polymer cells face diffusion challenges during high-rate discharges. |
Smith et al. | Highlighted lithium species depletion or saturation as key limiting factors. |
Hasan et al. | Suggested improved electrode designs to enhance rapid-charge performance. |
These findings underscore the importance of optimizing electrolyte composition and electrode design to overcome these limitations. For industrial-grade batteries, tailoring the electrolyte to specific operating conditions can significantly enhance charging efficiency.
3.3 Innovations in materials to enhance charging performance
Recent innovations in materials science aim to address the challenges of fast charging. Researchers have developed a novel electrolyte, tris(2-fluoroethyl) borate (TFEB), which improves the solubility and stability of lithium metal batteries. This advancement enables safer and more efficient operation under high-speed charging conditions. Additionally, artificial intelligence and machine learning are being used to accelerate the discovery of new electrolyte solvents, potentially revolutionizing energy storage solutions.
These breakthroughs not only improve the impact of fast charging but also contribute to the sustainability of lithium battery technology. By adopting cutting-edge materials and leveraging AI-driven research, you can achieve faster charging speeds while maintaining safety and extending battery life. For customized solutions tailored to your needs, consider consulting experts in the field. Learn more from Large Power.

Part 4: State of Charge (SOC) and Charging Speed of Lithium Battery
4.1 Why charging slows as the battery nears full capacity
As a lithium battery approaches full capacity, its charging speed decreases significantly. This slowdown occurs due to the transition from the constant current (CC) phase to the constant voltage (CV) phase. During the CC phase, the battery charges at a steady current. However, as the state of charge (SOC) increases, the voltage rises and reaches a threshold where the CV phase begins. In this phase, the current gradually decreases to prevent overcharging, ensuring battery health and safety.
The following table illustrates how SOC impacts the charge rate:
SOC Range | Charge Rate |
---|---|
0%-60% | C/2 (0.75 Amp) |
40%-100% | C/2 (0.75 Amp) |
20%-80% | 2C (3 Amp) discharge, C/2 (0.75 Amp) charge |
This data highlights the reduced charging times during the early SOC range compared to the later stages. Managing this slowdown is critical for applications requiring fast charging, such as industrial systems.
4.2 Voltage thresholds and their role in charging speed
Voltage thresholds play a pivotal role in determining the charging speed of lithium-ion batteries. Maintaining a voltage below 4.20V per cell is essential for prolonging battery life. Exceeding this threshold may enhance capacity temporarily but accelerates degradation, leading to reduced battery capacity and safety risks. During charging, the voltage increases steadily until it reaches this threshold, at which point the current begins to taper off.
This relationship between SOC and voltage is particularly evident during the CV phase. By carefully monitoring voltage thresholds, you can optimize charging speed while preserving battery health. Advanced battery management systems (BMS) are instrumental in achieving this balance, especially in applications like electric vehicles and industrial equipment.
4.3 SOC management for industrial battery packs
Effective SOC management is crucial for optimizing the performance of industrial lithium-ion battery packs. Advanced BMS technology enables accurate real-time SOC estimation, which is vital for maximizing battery lifetime and ensuring reliable operation. For instance, the use of extended Kalman filters has demonstrated significant improvements in SOC estimation accuracy, reducing errors by up to 85%.
Proper SOC management minimizes risks such as overcharging and overheating, which can lead to degradation and reduced battery capacity. It also ensures consistent performance across varying operational conditions. For industrial applications, adopting customized battery solutions tailored to specific SOC requirements can further enhance efficiency and safety. Explore tailored solutions for your needs from Large Power.
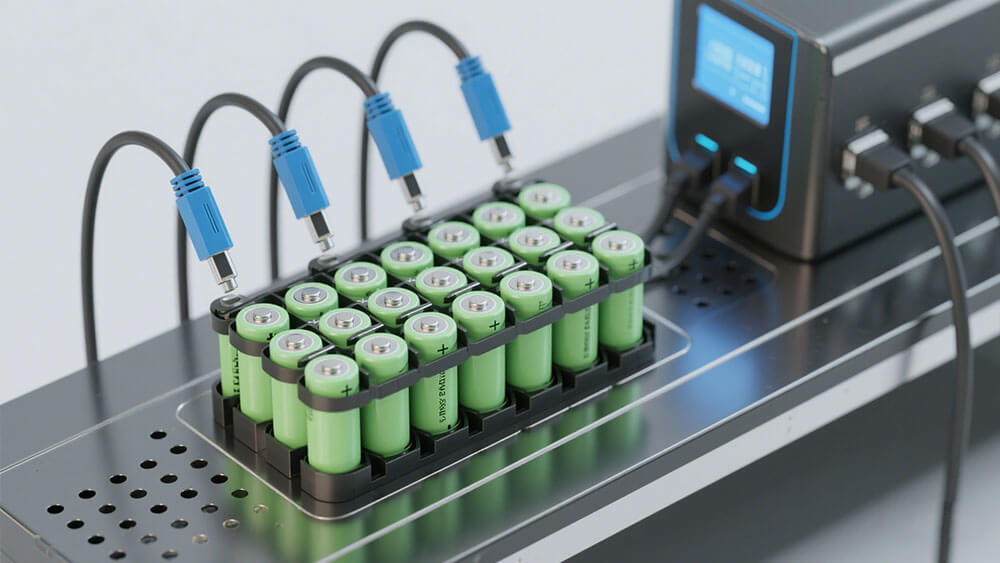
Part 5: Safety and Longevity of Lithium Batteries
5.1 Risks of lithium plating during fast charging
Fast charging introduces the risk of lithium plating, a phenomenon where metallic lithium deposits on the anode surface instead of intercalating into the electrode. This issue arises when the charging current exceeds the rate at which lithium ions can diffuse into the anode material. Lithium plating not only reduces the battery’s capacity but also poses significant safety risks, such as internal short circuits and thermal runaway.
You can mitigate this risk by carefully managing the charging current and temperature. Advanced battery management systems (BMS) play a crucial role in detecting and preventing conditions that lead to lithium plating. For industrial applications, selecting batteries with optimized anode materials, such as lithium-titanate (LTO), can further reduce the likelihood of plating. These materials offer faster lithium-ion diffusion rates, enhancing safety during high-speed charging.
5.2 Heat generation and its effect on battery lifespan
Heat generation during charging significantly impacts the lifespan of lithium-ion batteries. High temperatures accelerate chemical reactions within the battery, leading to faster degradation of the electrolyte and electrode materials. This degradation manifests as capacity loss, increased internal resistance, and reduced cycle life. The following table summarizes findings from various studies on heat-induced degradation:
Study Type | Findings |
---|---|
Pouch Cells | Inhomogeneous intra-cell degradation is common. |
Cylindrical Cells | Similar degradation patterns observed. |
Coin Cells | Degradation modes influenced by thermal gradients. |
Thermal Management | Effective management slows degradation processes in single-cell and battery packs. |
Active Cooling | Different cooling methods can affect degradation rates significantly, up to three times for high-power pouch cells. |
To minimize heat-related degradation, you should implement robust thermal management systems. These systems include passive cooling methods, such as heat sinks, and active cooling techniques, like liquid cooling. For high-power industrial battery packs, advanced cooling solutions can extend the battery’s operational life while maintaining performance.
5.3 Strategies to balance fast charging with long-term performance
Balancing fast charging with long-term performance requires a multi-faceted approach. One effective strategy involves the development of high-rate anode materials. Traditional materials, such as graphite, struggle with fast charging due to slow interfacial dynamics and the risk of lithium dendrite formation. Alternatives like silicon-carbon composites and lithium-titanate (LTO) offer improved charge acceptance and reduced degradation, making them suitable for high-speed charging applications.
Another critical aspect is optimizing the charging protocol. Adaptive charging algorithms, which adjust the current and voltage based on the battery’s state of charge (SOC) and temperature, can enhance both safety and longevity. For example, reducing the charging current during the constant voltage phase minimizes stress on the battery, preventing overcharging and thermal damage.
Case studies have shown that combining advanced materials with intelligent charging protocols yields significant benefits. These include faster charging times, extended cycle life, and improved safety. By adopting these strategies, you can achieve a balance between performance and durability, ensuring reliable operation in demanding industrial environments. For tailored solutions that meet your specific needs, consult experts in custom battery design from Large Power.
Lithium batteries face charging speed limitations due to internal resistance, temperature sensitivity, material constraints, and SOC effects. You can optimize performance by monitoring temperature, avoiding overcharging, and using advanced materials. For industrial applications, charging rates typically range from 1C to 3C, but SOC above 90% slows charging significantly due to increased resistance.
FAQ
1. How does fast charging affect the lifespan of lithium batteries?
Fast charging generates heat, which accelerates chemical degradation. This reduces the battery’s capacity and cycle life. Use thermal management systems to mitigate these effects.
2. Can you charge lithium batteries in freezing temperatures?
No, charging below 0°C risks lithium plating, which permanently damages the battery. Use industrial-grade chargers with safeguards to prevent charging in sub-zero conditions.
3. What is the safest way to fast charge lithium batteries?
Monitor temperature and state of charge (SOC). Use advanced battery management systems (BMS) and follow manufacturer-recommended charging protocols to ensure safety and longevity.