Contents
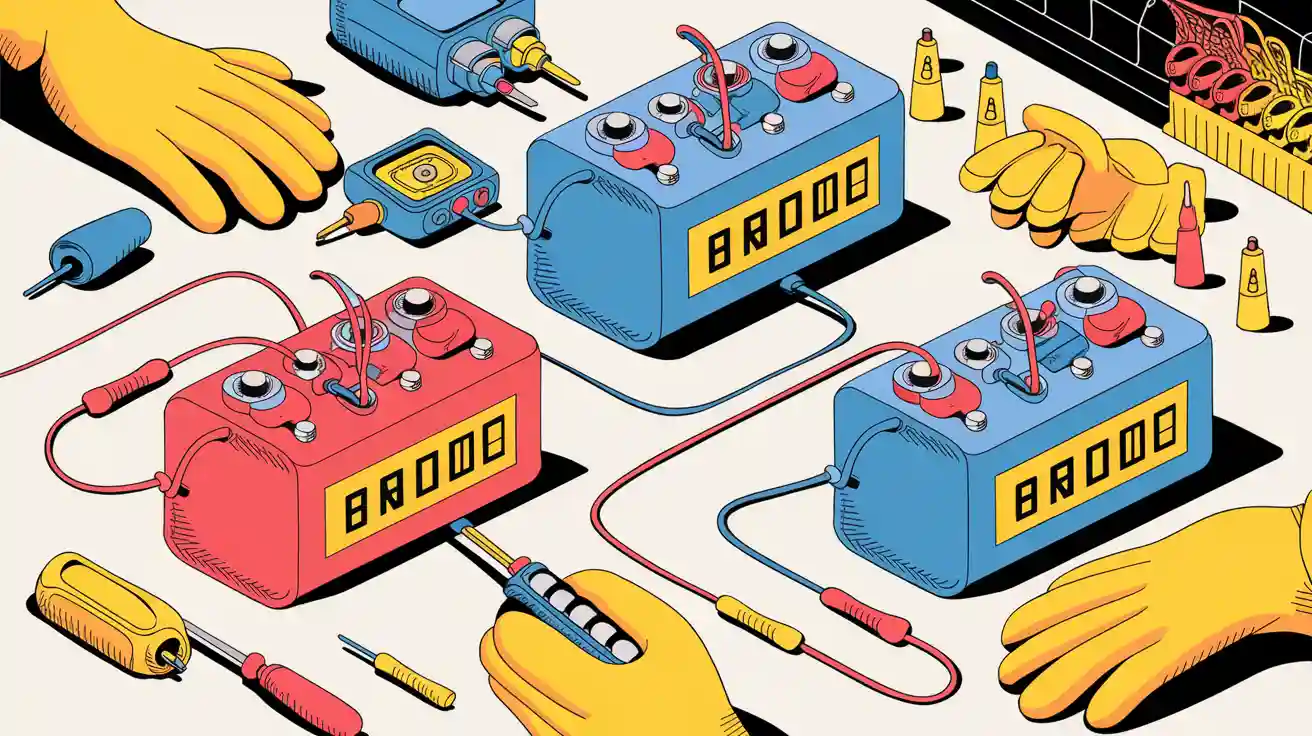
Safety is of utmost importance when working with a battery in series and parallel configurations. Incorrect handling can result in significant risks such as overcharging, thermal runaway, or cell imbalances. For example, even a small temperature rise of 2° can initiate thermal runaway, emphasizing the critical need for accurate monitoring. Adhering to best practices helps mitigate these risks and ensures greater operational reliability.
Key Takeaways
Always use a trusted Battery Management System (BMS). It checks voltage and stops overcharging or overdischarging.
Make sure all batteries have the same voltage, size, and type. This prevents dangers like overheating or thermal runaway.
Check battery connections often. Use cooling systems to control heat and stay safe.
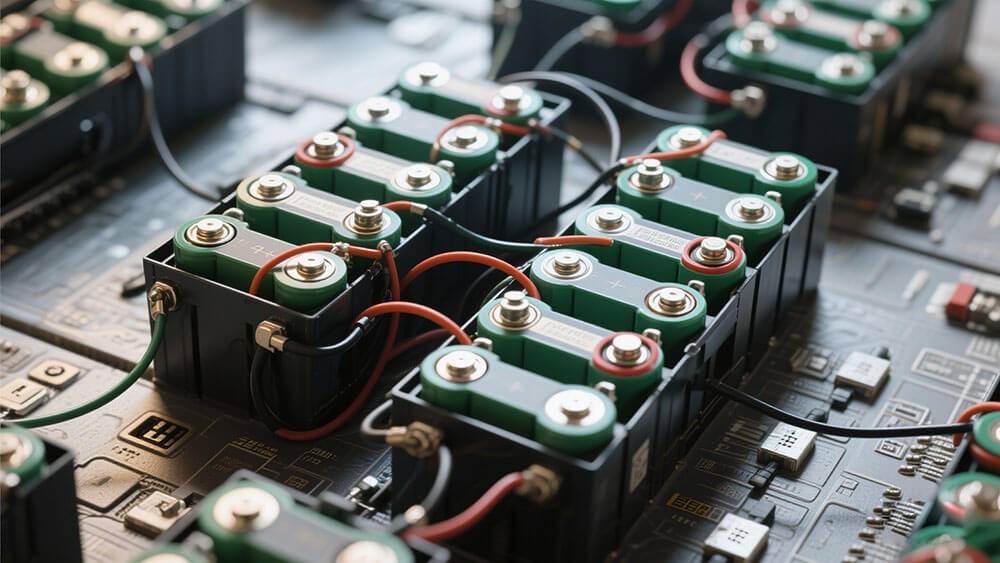
Part 1: Overview of Battery in Series and Parallel Configurations
1.1 Series Connection: Definition and Applications
A series connection involves linking batteries end-to-end, where the positive terminal of one battery connects to the negative terminal of the next. This configuration increases the total voltage while maintaining the same capacity as a single battery. For example, connecting three 3.7V lithium-ion batteries in series results in a total voltage of 11.1V, suitable for applications requiring higher voltage, such as power tools, electric vehicles, and industrial equipment. However, series configurations demand precise monitoring to prevent overcharging or overdischarging, as the weakest cell can limit the performance of the entire pack.
1.2 Parallel Connection: Definition and Applications
In a parallel connection, all positive terminals are connected, and all negative terminals are linked together. This setup keeps the voltage constant while increasing the total capacity. For instance, connecting three 3.7V lithium-ion batteries in parallel maintains a voltage of 3.7V but triples the capacity, extending the runtime. Parallel configurations are ideal for applications requiring longer operational periods, such as medical devices, robotics, and consumer electronics. Proper balancing circuits are essential to ensure even current distribution and mitigate safety concerns like uneven charging.
1.3 Key Differences Between Series and Parallel Configurations
The table below highlights the primary differences between series and parallel battery configurations:
Aspect | Series Configuration | Parallel Configuration |
---|---|---|
Voltage | Total voltage is the sum of individual cells. | Voltage remains constant at a single cell’s level. |
Capacity | Capacity remains the same as a single cell. | Total capacity is the sum of all cells. |
Failure Impact | A single cell failure interrupts the circuit. | Other cells continue functioning independently. |
Applications | High-voltage systems like EVs and tools. | Long-runtime systems like medical devices. |
In series configurations, the performance depends on the weakest cell, which can reduce the lifespan of the battery pack. Parallel configurations, on the other hand, distribute charge cycles more effectively, enhancing longevity. Both setups require robust battery management systems (BMS) to address safety concerns like thermal runaway and voltage imbalances.
Part 2: Safety Concerns in Series and Parallel Configurations
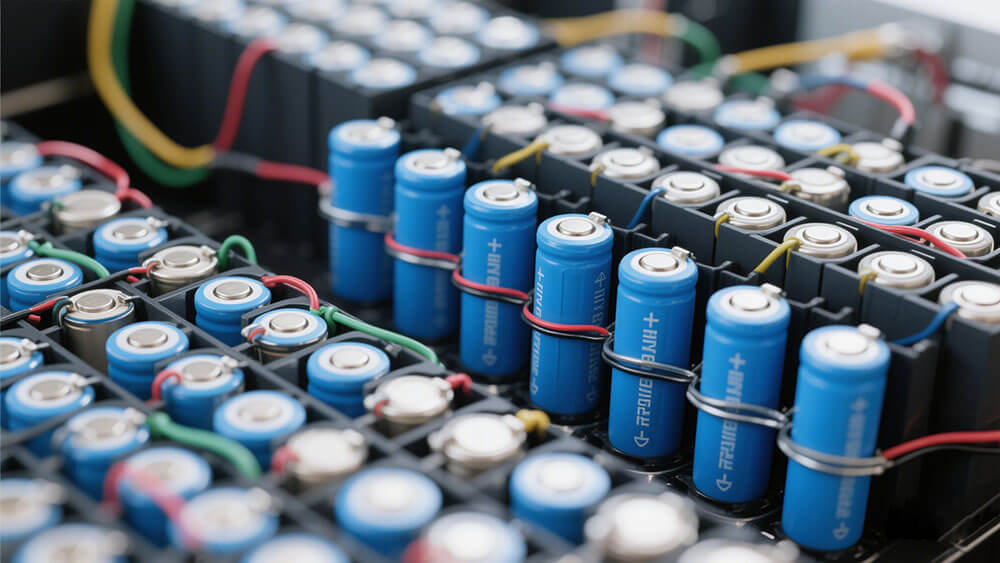
2.1 Overcharging and Overdischarging Risks
Overcharging and overdischarging represent two of the most critical risks when working with lithium-ion batteries. Overcharging occurs when a battery is charged beyond its maximum voltage limit, while overdischarging happens when the voltage drops below the safe threshold. Both scenarios can lead to severe consequences, including capacity degradation, internal short circuits, and even thermal runaway.
Overcharging by just 0.4V can significantly reduce battery life, shortening it to approximately 200 days. Additionally, overvoltage increases the likelihood of lithium plating, which can cause internal shorts and compromise safety. The financial impact of capacity loss in a 100kWh battery pack is substantial, with losses estimated at $200 per kWh. On the other hand, overdischarging triggers side reactions that degrade the battery’s capacity and lifespan. These reactions may result in solid-state amorphization of transition metal compounds, further increasing the risk of internal short circuits.
Evidence | Description |
---|---|
Impact of Overcharging | Overcharging at 0.4V can lead to capacity fade, shortening battery life. |
Li-Plating Potential | Increased overvoltage decreases Li-plating potential, raising safety risks. |
Financial Impact | Capacity loss in a 100kWh pack can cost $200/kWh. |
To mitigate these risks, you should always use a reliable battery management system (BMS). A BMS monitors voltage levels and prevents overcharging or overdischarging, ensuring the longevity and safety of your battery packs.
2.2 Thermal Runaway: Causes and Prevention
Thermal runaway is one of the most dangerous safety concerns in lithium-ion batteries. It occurs when a battery’s internal temperature rises uncontrollably, leading to a chain reaction that can result in fire or explosion. Between 2019 and 2023, thermal runaway incidents increased by 28%, with an average of two incidents reported weekly. While 85% of these cases were addressed before escalating to fire or explosion, the remaining incidents highlight the critical need for preventive measures.
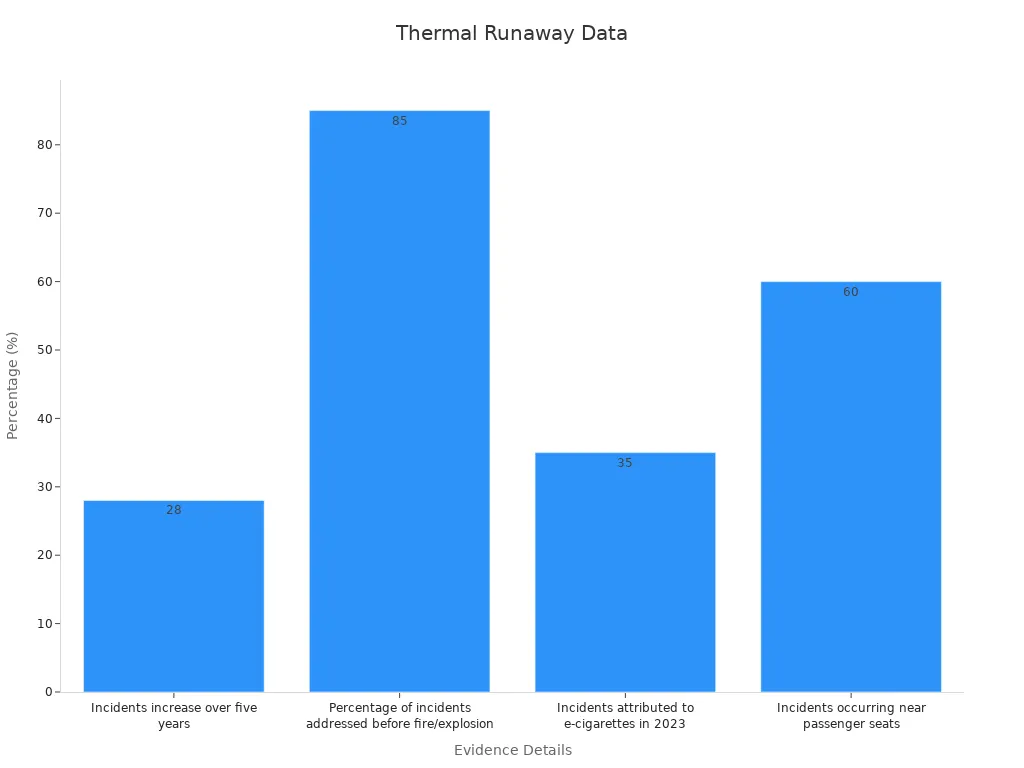
Several factors contribute to thermal runaway, including external abuse, internal short circuits, and heat transfer within battery packs. Prevention techniques focus on minimizing these triggers. For example, using noncombustible materials and flame retardants can reduce the risk of internal short circuits. Adding epoxy resin plates and safety-reinforced layers can block thermal conduction, preventing heat from spreading across the battery pack.
Causes of Thermal Runaway | Prevention Techniques |
---|---|
External battery abuse | Insulation |
Internal short circuits | Noncombustible materials, flame retardants |
Heat transfer in battery packs | Safety-reinforced layers, epoxy resin plates |
By implementing these strategies, you can significantly reduce the likelihood of thermal runaway and enhance the safety of your battery systems.
2.3 Hazards of Mismatched Cells in Lithium Battery Packs
Mismatched battery cells pose significant hazards in both series and parallel configurations. Variations in voltage, capacity, or internal resistance among cells can lead to uneven charging and discharging. This imbalance increases the risk of overheating, overcharging, and thermal runaway.
For instance, in a series configuration, the weakest cell determines the overall performance of the pack. If one cell becomes overcharged, it can trigger a chain reaction, compromising the entire system. In parallel configurations, mismatched cells can cause uneven current distribution, leading to localized overheating and potential failure.
To avoid these hazards, always ensure that all cells in a battery pack match in terms of voltage, capacity, and chemistry. Using a BMS with cell-balancing capabilities can further mitigate these risks by equalizing the charge and discharge rates across all cells.
2.4 Short Circuits and Electrical Safety Risks
Short circuits are another critical safety concern when connecting batteries. They occur when a low-resistance path forms between the positive and negative terminals, allowing excessive current to flow. This can result in overheating, thermal runaway, or even explosions.
Short circuits often arise from damaged insulation, improper wiring, or external conductive materials coming into contact with the terminals. To minimize these risks, you should:
Use high-quality insulation materials to protect wiring.
Ensure proper spacing between terminals to prevent accidental contact.
Regularly inspect battery packs for signs of wear or damage.
Additionally, integrating circuit protection devices, such as fuses or circuit breakers, can provide an added layer of safety. These devices interrupt the current flow in the event of a short circuit, preventing further damage to the battery pack.
By addressing these safety risks and implementing robust mitigation strategies, you can ensure the reliable and safe operation of your lithium battery systems.
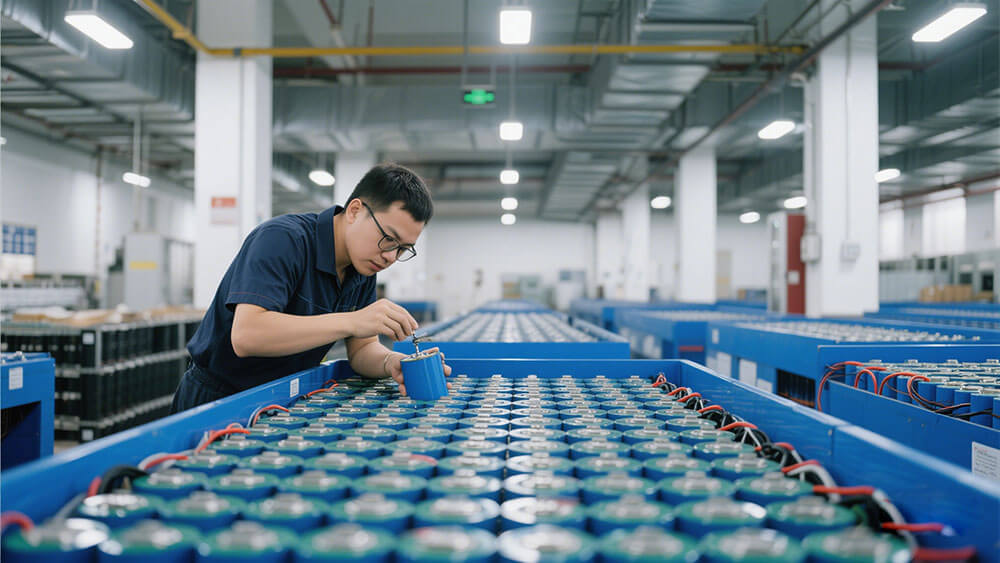
Part 3: Safety Risks and Mitigation Strategies
3.1 Importance of Using a Battery Management System (BMS)
A Battery Management System (BMS) plays a pivotal role in ensuring the safety and efficiency of lithium battery packs, especially in series and parallel configurations. It acts as the brain of the battery system, monitoring critical parameters like voltage, current, and temperature to prevent potential hazards.
“Implementing a reliable Battery Management System is crucial when working with parallel configurations,” states Dr. Jane Smith, an expert in energy storage solutions. “It not only enhances safety but also ensures that your entire battery system operates efficiently and lasts longer.”
Key benefits of using a BMS include:
Improved Reliability: It ensures all cells operate within their safe limits, reducing the risk of imbalances.
Increased Efficiency: By balancing charge levels, the system optimizes the performance of the battery pack.
Simplified Maintenance: A BMS provides alerts and diagnostics, making it easier to identify and address issues.
In series configurations, a BMS prevents overcharging or overdischarging of individual cells, which could lead to thermal runaway. For parallel setups, it ensures voltage balancing, preventing one cell from overcharging or discharging faster than others. Without a BMS, the risks of skipping a parallel charging board increase significantly, jeopardizing the safety of the entire system.
3.2 Ensuring Proper Ventilation and Cooling Systems
Effective ventilation and cooling systems are essential for maintaining the thermal stability of lithium battery packs. Heat buildup during charging or discharging can lead to thermal runaway, especially in high-capacity applications like industrial equipment or electric vehicles.
To ensure proper cooling:
Install ventilation ducts to dissipate heat generated during operation.
Use active cooling systems, such as fans or liquid cooling, for high-power applications.
Incorporate thermal insulation materials to prevent heat transfer between cells.
A well-designed cooling system not only prevents overheating but also extends the lifespan of the battery pack. For example, maintaining an optimal operating temperature can reduce the risk of voltage and current imbalances, ensuring consistent performance across all cells.
3.3 Matching Battery Specifications: Voltage, Capacity, and Chemistry
Matching battery specifications is critical for the safe and efficient operation of series and parallel configurations. Variations in voltage, capacity, or chemistry among cells can cause imbalances, leading to uneven charging and discharging.
Voltage Alignment: Lithium battery cells have specific voltages based on their chemistry, such as 3.2V for LiFePO4 or 3.7V for LCO. Ensure all cells in a pack have the same nominal voltage to avoid overcharging or overdischarging.
Capacity Matching: Cells with different capacities will charge and discharge at different rates, increasing the risk of overheating.
Chemistry Consistency: Mixing different chemistries, such as NMC and LMO, can lead to chemical reactions that compromise safety.
Proper alignment of these specifications ensures optimal performance and reduces the risk of voltage and current imbalances. When connecting batteries, always verify their specifications to prevent potential hazards.
3.4 Regular Inspection and Maintenance Protocols
Regular inspection and maintenance are vital for identifying and addressing potential issues in lithium battery packs. Neglecting maintenance can lead to undetected imbalances, increasing the risk of failure or safety incidents.
Follow these maintenance protocols:
Visual Inspection: Check for signs of physical damage, such as swelling or corrosion.
Voltage Monitoring: Measure the voltage of each cell to detect imbalances early.
Thermal Scanning: Use infrared cameras to identify hotspots within the battery pack.
Connection Check: Ensure all terminals and connectors are secure and free of debris.
Establishing a routine maintenance schedule helps you detect and resolve issues before they escalate. For large-scale applications, consider integrating advanced precautions for optimal performance, such as automated diagnostic tools or predictive maintenance systems.
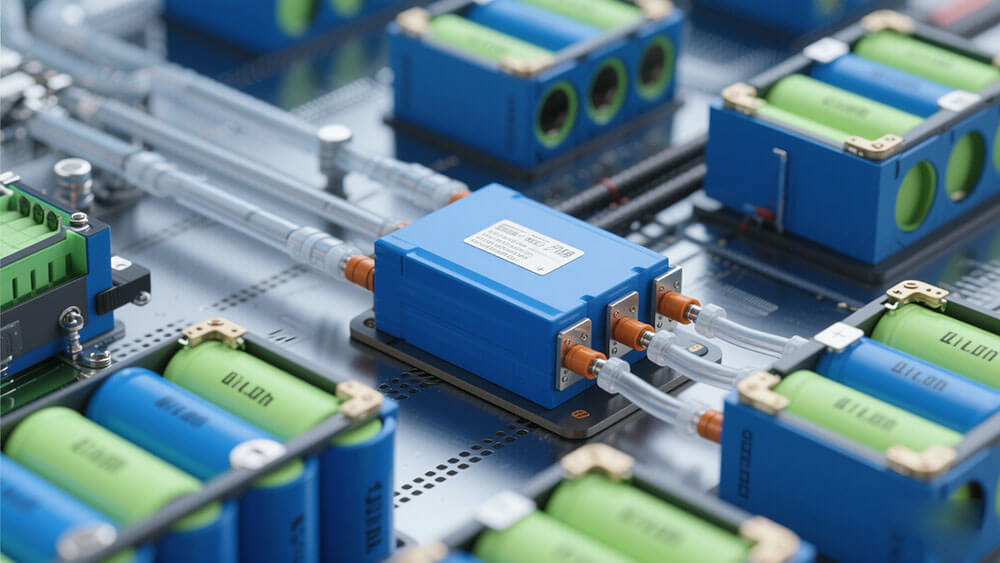
Part 4: Step-by-Step Safety Protocols for Connecting Batteries
4.1 Tools and Materials Required for Safe Connections
To safely connect batteries in series or parallel, you need specific tools and materials. These include insulated wires, a multimeter for voltage checks, and a reliable Battery Management System (BMS). Use high-quality connectors to ensure secure and stable connections. Additionally, have heat-resistant gloves and safety goggles to protect yourself from potential hazards during the process.
Tip: Always work in a well-ventilated area to prevent overheating and ensure proper dissipation of heat generated during connections.
4.2 Step-by-Step Guide for Connecting Batteries in Series
Follow these steps to connect batteries in series safely:
Arrange the batteries so their terminals align for easy access.
Connect the positive terminal of the first battery to the negative terminal of the next battery using a jumper wire.
Repeat this process for all batteries in the series.
Leave the remaining positive and negative terminals open for connection to the load or charger.
Warning: Never cross the open positive and negative terminals, as this can cause a short circuit and damage the batteries.
4.3 Step-by-Step Guide for Connecting Batteries in Parallel
To connect batteries in parallel, follow these steps:
Ensure all batteries have the same voltage and capacity. Use a multimeter to confirm they are within 0.1V of each other.
Connect all positive terminals together using jumper wires.
Link all negative terminals in the same manner.
Use a BMS to monitor and balance the voltage across the batteries.
Pro Tip: Install fuses on each battery’s positive terminal to enhance safety and prevent overcurrent issues.
4.4 Testing and Verifying Connections for Safety
After completing the connections, test the setup to ensure safety and functionality:
Use a multimeter to check the total voltage of the series or parallel configuration. Verify that it matches the expected value.
Inspect all connections for tightness and ensure no wires are exposed.
Perform a load test by connecting a device to the battery pack and monitoring its performance.
Regular testing and verification help identify potential issues early, ensuring the longevity and safety of your battery system.
4.5 Balancing Strategies for Series and Parallel Configurations
Balancing is crucial for maintaining the performance and safety of battery packs. Use the following strategies:
Balancing Strategy | Description |
---|---|
Dissipative Balancing | Discharges cells with higher voltage using resistors to equalize the state of charge. |
Resistor Sizing | Align resistor size with the charger’s lowest power to prevent overcharging. |
Thermal Management | Incorporate cooling systems to prevent overheating during balancing. |
Implementing these strategies ensures even load distribution, reducing the risk of overheating and extending the lifespan of your battery pack.
Adhering to safety protocols when connecting batteries in series or parallel is essential for preventing risks like thermal runaway and overcharging. Use proper tools, such as a reliable Battery Management System (BMS), to ensure safe and efficient operations.
Key Safety Tips:
Match battery specifications, including voltage and capacity.
Regularly inspect connections and monitor for imbalances.
Implement robust cooling systems to manage heat effectively.
Electric vehicle fire rates (0.025%) are significantly lower than those of gasoline-powered cars (3.5%), highlighting the importance of compliance and monitoring in battery systems.
For tailored solutions, consult professionals like Large Power to optimize your battery configurations. Explore Large Power custom battery solutions for expert guidance.
FAQ
1. What is the role of a Battery Management System (BMS) in lithium battery packs?
A BMS monitors voltage, current, and temperature, ensuring safe operation. It prevents overcharging, overdischarging, and imbalances in series or parallel configurations. Learn more at Large Power.
2. Can mismatched cells be used in a lithium battery pack?
No, mismatched cells cause uneven charging, overheating, and reduced lifespan. Always match voltage, capacity, and chemistry to ensure safety and performance.
3. How can thermal runaway be prevented in lithium battery systems?
Use noncombustible materials, flame retardants, and cooling systems. Regularly inspect for damage and integrate a reliable BMS to monitor temperature and voltage fluctuations.