Contents
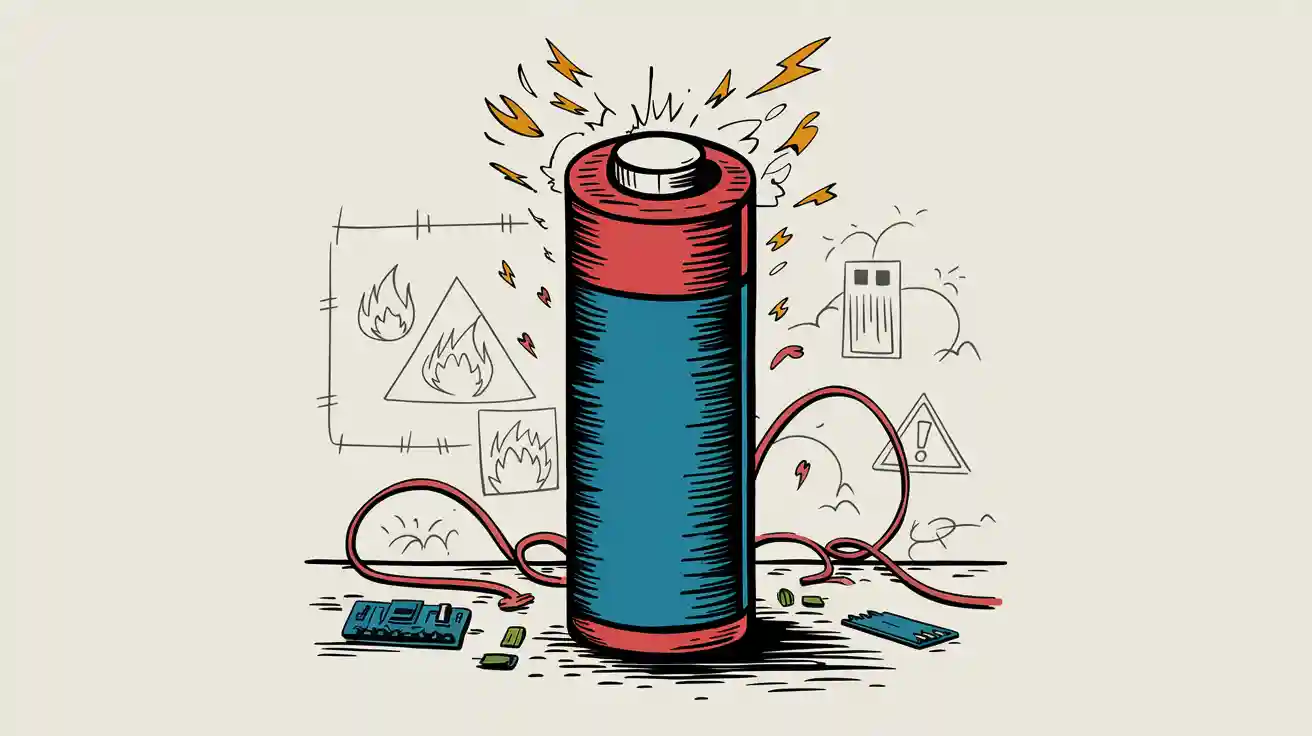
Lithium-ion batteries have revolutionized industries by powering critical applications in medical devices, robotics, and infrastructure. For instance, they enable portable monitors and surgical tools in medical settings, and delivery robots rely on their efficiency. However, the risks associated with a short circuit of lithium battery, such as fires or operational failures, demand your attention. Why do these batteries face such vulnerabilities, and what are the consequences when a short circuit occurs?
Key Takeaways
Lithium-ion batteries power many devices but can be dangerous. Fires or explosions may happen if they short circuit.
Avoid short circuits by handling, storing, and transporting batteries carefully. Buy batteries from trusted brands.
Use smart Battery Management Systems (BMS) to check battery health. These systems stop overheating, which can cause serious problems.
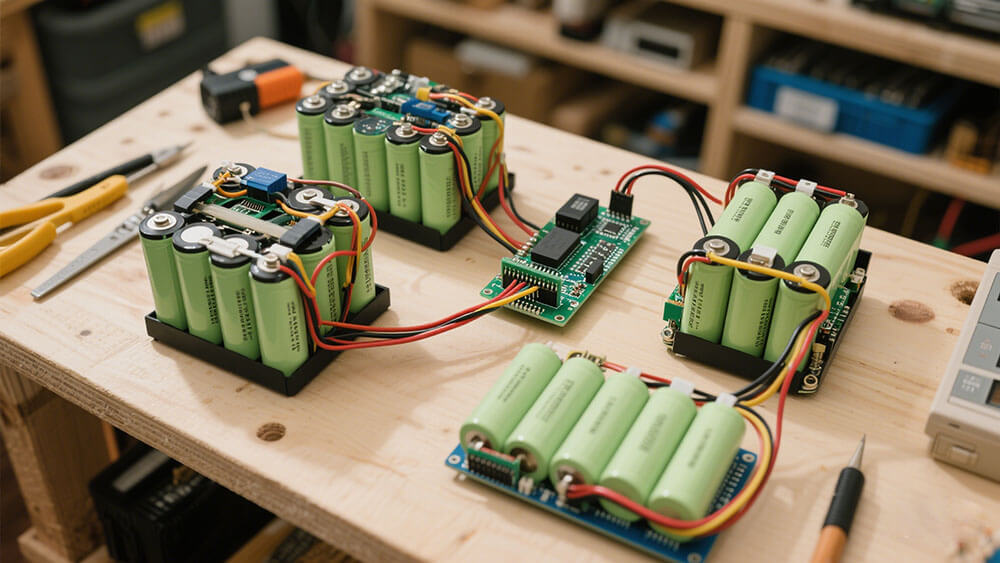
Part 1: Understanding Lithium-Ion Batteries and Their Vulnerabilities
1.1 Key Components of Lithium-Ion Batteries
Lithium-ion batteries consist of several critical components that work together to deliver reliable energy storage. These include:
Electrodes: The positive electrode (cathode) and negative electrode (anode) facilitate the movement of lithium ions during charging and discharging cycles.
Electrolyte: This liquid medium enables ion transport between electrodes, ensuring efficient energy transfer.
Separator: Positioned between the electrodes, the separator prevents direct contact, reducing the risk of short circuits of lithium batteries.
Battery Management System (BMS): This system monitors and regulates battery performance, enhancing safety and protection against overheating or overcharging.
Despite their high reliability, with failure rates as low as one in 10 million cells, lithium-ion batteries remain susceptible to issues under extreme conditions. Abuse tests, such as nail penetration and thermal abuse, have demonstrated vulnerabilities in commercial lithium battery designs.
1.2 Why Lithium-Ion Batteries Are Prone to Short Circuits
Lithium-ion batteries are prone to short circuits due to internal and external factors. Research shows that localized temperature hotspots accelerate lithium growth, leading to dendritic formations that pierce the separator. This phenomenon increases the risk of lithium battery short circuit events. Additionally, electrolyte leakage, electrode damage, and improper handling during transportation can compromise battery integrity.
Short circuits during transportation or charging often result from external metal contact or separator failure. These incidents can trigger thermal runaway, where excessive heat causes uncontrollable reactions, leading to fires or explosions.
1.3 The Role of Battery Packs in Mitigating Risks
Battery packs play a vital role in reducing the risks associated with lithium batteries short circuit events. Advanced designs integrate protective features such as thermal management systems and reinforced separators. According to the Electric Power Research Institute (EPRI), battery energy storage system failures have decreased significantly, from over nine failures per gigawatt in 2018 to less than one failure per gigawatt in 2023.
This improvement highlights the effectiveness of battery packs in mitigating risks and enhancing operational safety. By adopting customized battery solutions, you can ensure optimal performance and reduce the likelihood of lithium battery short circuit incidents. Explore tailored solutions from Large Power to meet your specific needs.
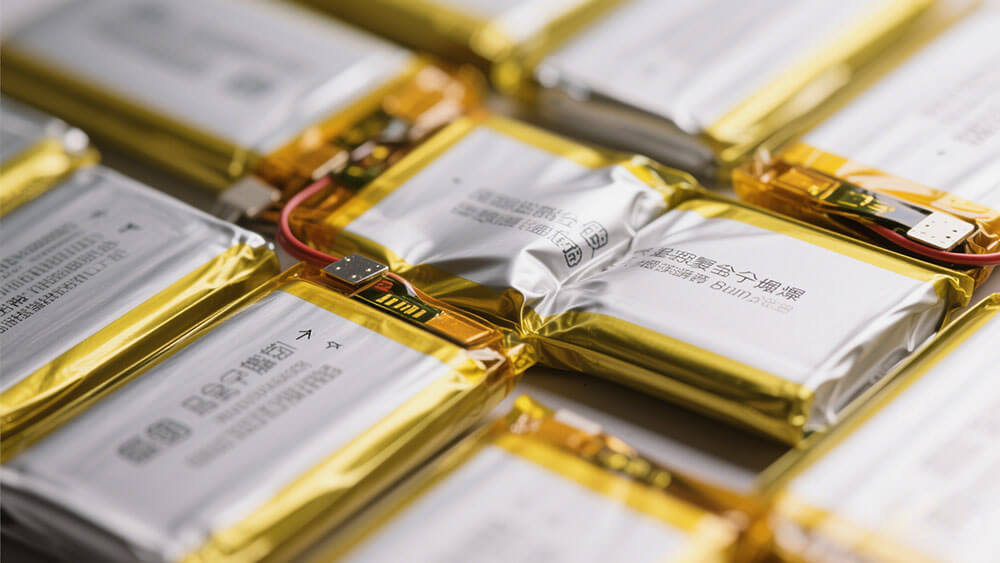
Part 2: Causes of Lithium Battery Short Circuits
2.1 Internal Factors: Manufacturing Defects and Dendritic Growth
Manufacturing defects remain a significant contributor to lithium battery short circuit incidents. These defects often stem from inconsistencies in electrode alignment, separator quality, or electrolyte composition. Even minor imperfections can compromise the battery’s structural integrity, increasing the likelihood of internal failures.
Dendritic growth, a phenomenon where lithium deposits form needle-like structures during repeated charging cycles, poses another critical risk. These dendrites can pierce the separator, creating direct contact between electrodes and triggering a short circuit of lithium battery. Studies have revealed that localized temperature hotspots accelerate dendrite formation, especially in high-energy-density batteries. Numerical simulations further highlight how factors like current density and electrolyte composition influence dendrite growth. Monitoring and detecting these formations early can significantly enhance battery safety and prevent catastrophic failures.
2.2 External Factors: Physical Damage and Improper Handling
Physical damage and improper handling during transportation or usage frequently lead to lithium battery short circuit events. Rough handling, such as dropping or puncturing battery packs, can compromise the separator or electrodes, initiating thermal runaway. Incident reports from the FAA confirm that mishandling lithium-ion batteries during transit has resulted in fires and explosions.
Improper handling also includes using unregulated or counterfeit battery packs, which lack essential protection mechanisms. For example:
A major e-bike battery fire in the Bronx destroyed a supermarket, highlighting the dangers of mishandling.
The FDNY Commissioner emphasized the risks associated with unregulated battery packs, linking them to severe fire incidents.
To mitigate these risks, you should prioritize robust packaging and adopt certified battery solutions tailored to your operational needs.
2.3 Environmental Influences: Moisture, Dust, and Contaminants
Environmental factors like moisture, dust, and contaminants can degrade lithium batteries over time, increasing the risk of short circuits. Moisture exposure corrodes electrodes, while dust particles can infiltrate the separator, disrupting ion flow. Contaminants in the electrolyte further exacerbate these issues, leading to leakage and reduced battery performance.
Extreme environmental conditions, such as high humidity or temperature fluctuations, amplify these risks. For instance, batteries stored in poorly ventilated areas may experience accelerated degradation, compromising their safety and reliability. Implementing proper storage protocols and environmental controls can help you safeguard your battery packs against these influences.
2.4 Thermal Runaway: Overheating and Overcharging
Thermal runaway represents one of the most dangerous consequences of lithium battery short circuit incidents. Overcharging and overheating are primary triggers for this phenomenon. When a battery exceeds its thermal threshold, chemical reactions within the cell become uncontrollable, releasing excessive heat and gases. Signs of thermal runaway include bulging, mechanical damage, and visible venting.
Cycling and aging further contribute to battery degradation, making older batteries more susceptible to overheating. Research indicates that overcharging not only accelerates this process but also increases the risk of fire and explosion. To prevent thermal runaway, you should integrate advanced Battery Management Systems (BMS) into your battery packs. These systems monitor temperature and voltage levels, providing real-time protection against overheating and overcharging.
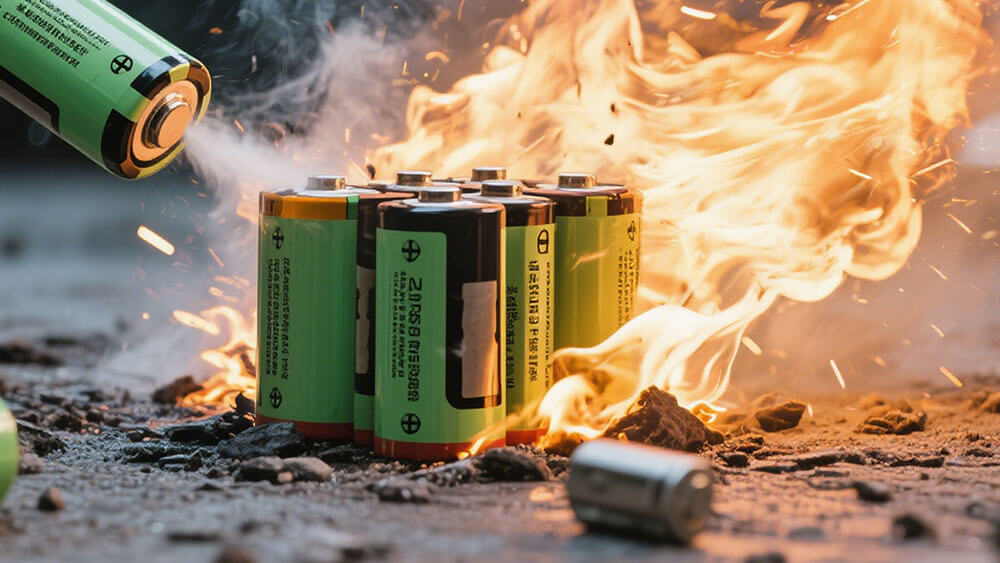
Part 3: Dangers of Short Circuiting Lithium Batteries
3.1 Safety Hazards: Fires, Explosions, and Chemical Leaks
Short circuits of lithium batteries pose significant safety risks, including fires, explosions, and chemical leaks. These hazards arise from the flammable and reactive nature of the battery’s components. When a short circuit occurs, the separator fails, allowing direct contact between electrodes. This contact generates excessive heat, which can ignite the electrolyte or release flammable gases.
Fire Risks: Lithium-ion batteries are particularly prone to fires due to their high energy density. Common warning signs include swelling, discoloration, and excessive heating. If ignored, these indicators can escalate into thermal runaway, leading to uncontrollable fires.
Explosions: A breached battery cell can release gases under high pressure, resulting in an explosion. This risk is amplified in confined spaces, such as during air transportation, where the consequences can be catastrophic.
Chemical Leaks: Leakage of the electrolyte not only damages the battery pack but also poses health risks. The chemicals released can corrode nearby materials and harm individuals exposed to them.
To mitigate these risks, you should implement robust safety measures, such as integrating advanced Battery Management Systems (BMS) and using certified battery packs. These systems monitor temperature and voltage, providing real-time protection against overheating and overcharging.
3.2 Operational Impacts: Damage to Battery Packs and Systems
The dangers of short circuiting lithium batteries extend beyond safety hazards to operational disruptions. Damaged battery packs can compromise the performance of critical systems, leading to costly downtime and repairs.
In 2023, over 200 incidents involving lithium-ion battery packs were reported aboard aircraft. These incidents highlight the operational risks associated with battery fires and thermal runaway.
Devices such as e-cigarettes, cell phones, and laptops accounted for additional incidents, emphasizing the widespread impact of battery failures across industries.
Thermal runaway, a common consequence of short circuits, can cause internal temperatures to reach 1,300°F. This extreme heat damages not only the battery but also the surrounding equipment. John Cox, a retired airline pilot, noted that user-induced damage, such as dropping devices or using non-OEM chargers, significantly increases the likelihood of such failures.
To ensure operational reliability, you should prioritize high-quality battery solutions tailored to your specific needs. Customized battery packs from Large Power offer enhanced protection and durability, reducing the risk of system failures.
3.3 Financial and Environmental Consequences
The financial and environmental consequences of lithium battery short circuits are substantial. From repair costs to environmental degradation, these incidents have far-reaching implications.
Financial Losses: Repairing or replacing damaged battery packs and systems can be expensive. Additionally, operational downtime caused by battery failures can result in lost revenue.
Environmental Impact: The production of lithium-ion batteries contributes significantly to carbon emissions, with 40% of the climate impact stemming from mining and processing minerals. Improper disposal exacerbates this issue, as 98.3% of lithium-ion batteries end up in landfills. These batteries can cause landfill fires, with one site reporting 124 fires over three years.
To address these challenges, you should adopt sustainable practices, such as recycling and using eco-friendly battery solutions. Learn more about sustainability initiatives at Large Power.
By understanding the dangers of short circuiting lithium batteries, you can take proactive steps to enhance safety, protect operations, and minimize environmental impact. Explore customized solutions from Large Power to meet your operational and sustainability goals.
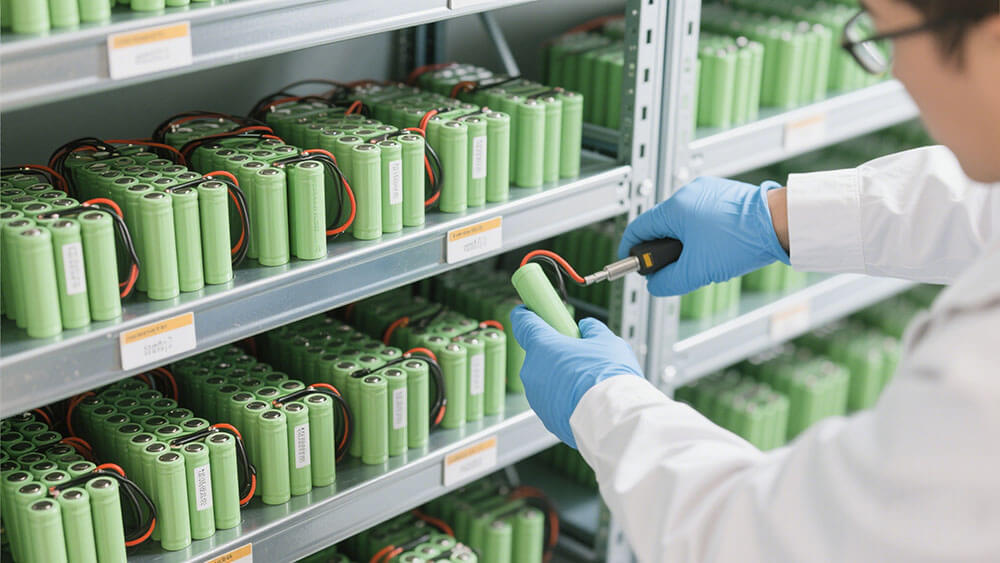
Part 4: Preventing Lithium Battery Short Circuits
4.1 Best Practices for Manufacturing and Quality Control
Adopting stringent manufacturing and quality control practices is essential to minimize the risk of short circuits in lithium-ion batteries. Key parameters during production ensure consistent performance and safety.
Key Factors and Parameters | Description |
---|---|
Electrode Uniformity | Ensures consistent performance across cells. |
Component Dryness | Prevents moisture-related issues in battery performance. |
Electrode Alignment | Critical for optimal cell function. |
Internal and External Pressure | Maintains structural integrity during operation. |
Electrolyte Amount Control | Essential for battery efficiency and safety. |
Cell Fixture with Pressure Control | Ensures uniform pressure distribution during manufacturing. |
Advanced analytical techniques, such as Raman spectroscopy, play a pivotal role in quality control. This method enables bulk analysis of lithium compounds and enhances manufacturing processes. By implementing these best practices, you can significantly reduce the likelihood of defects that lead to short circuits of lithium batteries.
4.2 Proper Handling, Storage, and Transportation
Proper handling, storage, and transportation are critical to preventing fires and other hazards. Follow these guidelines to ensure safety:
Purchase batteries from reputable manufacturers to guarantee quality.
Store batteries away from combustible materials like paper or fabric.
Remove batteries from devices if stored for extended periods to prevent leakage.
Maintain recommended storage temperatures to avoid degradation.
Separate fresh and depleted cells to prevent accidental use of depleted batteries.
Use metal storage cabinets for added safety, if feasible.
Regularly inspect batteries for damage, swelling, or leakage.
Keep batteries partially charged (around 50%) during storage.
Safe handling practices, such as avoiding contact with conductive materials, are vital. These measures prevent short circuits and ensure operational reliability.
4.3 The Role of Battery Management Systems (BMS)
Battery Management Systems (BMS) are indispensable for protecting lithium-ion batteries from thermal runaway and overcharging. These systems monitor voltage, temperature, and current in real-time, ensuring optimal performance. Overcharging often leads to thermal runaway, which can cause fires or explosions. A robust BMS prevents this by cutting off the charging current when the battery reaches full capacity. Numerous safety incidents in electric vehicles highlight the importance of integrating advanced BMS into battery packs. Learn more about BMS technology here.
4.4 Regular Maintenance and Inspection of Battery Packs
Routine maintenance and inspections are crucial for extending battery life and reducing the risk of short circuits. Regular practices include visual inspections, resistance testing, and electrolyte checks. Adhering to standards from organizations like IEEE ensures inspections occur at appropriate intervals. Frequent inspections help identify potential issues early, enhancing battery performance and longevity. By prioritizing maintenance, you can safeguard your operations and minimize downtime caused by battery failures.
Understanding the causes and dangers of lithium battery short circuits is essential for ensuring safety and operational efficiency. Factors like manufacturing defects, physical damage, and thermal runaway can lead to severe risks, including fire hazards and system failures. Preventive measures, such as advanced quality control, robust Battery Management Systems (BMS), and flame-retardant materials, significantly reduce these risks.
Customized battery solutions, incorporating features like arc fault testing and temperature sensors, enhance safety and reliability. By adopting tailored solutions from Large Power, you can mitigate risks, protect your operations, and achieve long-term sustainability.
FAQ
1. What are the primary causes of lithium battery short circuits?
Manufacturing defects, dendritic growth, physical damage, and environmental factors like moisture or dust contribute to short circuits. Learn more about prevention here.
2. How can Battery Management Systems (BMS) prevent thermal runaway?
BMS monitors voltage, temperature, and current in real-time, cutting off charging when thresholds are exceeded.
3. Why should businesses consider customized battery solutions?
Tailored solutions enhance safety, operational reliability, and sustainability. Discover how Large Power can meet your needs here.