Contents
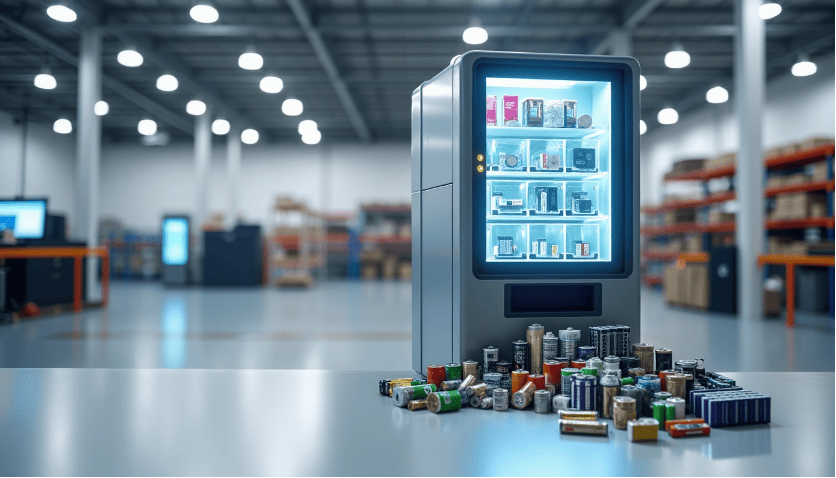
Call2Recycle has transformed battery recycling in North America. The program has processed nearly 170,000 cellphones and 8 million pounds of lithium-ion batteries since 2013. The country’s largest consumer battery stewardship program maintains 30,000 collection sites throughout the United States and Canada. Battery disposal is now available to 88% of North Americans who live within 10 miles of a drop-off location.
The program’s steadfast dedication to advancing lithium ion battery recycling technology has produced groundbreaking recycling solutions for growing environmental challenges. The closed-loop recycling system ensures that valuable materials like cobalt from used batteries help manufacture new ones and strengthen the recycling market. This detailed system now accepts household batteries of all types under 11 pounds, including both rechargeable and single-use batteries, paving the way to green battery disposal practices.
Call2Recycle Unveils Revolutionary Smart Collection Technology
Call2Recycle has launched North America’s first smart battery recycling container system. This revolutionary advancement in battery collection technology blends innovative technology with eco-friendly practices to improve operational efficiency and safety protocols.
How the Smart System Identifies Battery Types
The system uses advanced X-ray technology to identify and sort different battery chemistries, even with unidentifiable labels. The sorting technology automates battery chemistry identification tasks and enables efficient separation for recycling. Machine learning algorithms help the system recognize physical and chemical characteristics of battery types, especially when dealing with lithium-ion batteries.
Electronic Distributors International’s facility houses an automated sorting process that handles up to 500 kilograms of batteries per hour. This output doubles what traditional sorting lines can achieve. The system focuses on small, single-use batteries like AA, AAA, 9V, C, D, and button batteries, which make up 80% to 85% of Call2Recycle’s program volume.
Real-time Monitoring Capabilities
Smart containers come equipped with sophisticated remote monitoring capabilities that improve safety measures throughout collection. Built-in sensors track container fill levels and notify program managers when pickup becomes necessary. The system also monitors temperature changes to detect potential thermal events and reduce safety risks.
The platform uses Microsoft Dynamics and Power Platform to streamline scheduling, routing, and logistics. Full containers trigger Power Automate flow, which creates service requests in Dynamics Sales. On-site vendors can fulfill these requests through a mobile Power Pages portal.
Call2Recycle’s Software as a Service solution, GreenTraxEV platform, offers detailed battery management features including:
- Training verification and safety checks
- Container assignment and tracking
- Automated routing and shipping management
- Battery tracking and invoicing systems
This intelligent system allows centralized decision-making while adapting to unexpected events like market changes or transportation disruptions. Smart containers placed at multiple municipal sites improve access to battery recycling services. Collection routes optimize to minimize carbon footprint.
Strategic collaborations with industry leaders like Chervon, Husqvarna, Makita, Stanley Black & Decker, STIHL, Techtronic Industries, and The Toro Company help Call2Recycle expand its network of smart collection points. These partnerships give consumers convenient access to responsible end-of-life battery solutions while supporting a circular economy in battery recycling.
Smart System Enhances Lithium Battery Safety Protocols
Call2Recycle’s smart collection system uses state-of-the-art X-ray technology that measures safety standards in lithium battery recycling. The system can process up to 500 kilograms of batteries per hour [1]. This creates resilient safety protocols for collection networks everywhere.
Automated Sorting Reduces Human Error
X-ray technology in the automated sorting system tackles a major challenge in battery recycling. It identifies each battery type accurately, even when labels cannot be read [1]. This automation reduces sorting errors and wrong chemistry identification that could cause safety incidents. Research shows automated sorting works better than manual methods, particularly when processing high-cobalt batteries [2].
Advanced Fire Prevention Features
Multiple layers of safety protocols create a complete fire prevention system. Temperature monitoring happens through thermal detection systems and backup manual readings during operations [3]. The facility has fire-resistant storage areas with Class D fire extinguishers placed away from structures [3]. Thermal barriers and fire suppression mechanisms work together to protect against potential heat-related events.
Emergency Response Integration
The smart system has sophisticated emergency response capabilities that meet United States Department of Transportation compliance procedures [4]. A 24-hour response line connects the system with local authorities during emergencies [4]. The program has special containment protocols for damaged, defective, or recalled batteries. These use approved containers that meet DOT’s Pipeline and Hazardous Materials Safety Administration requirements [5].
The system’s emergency protocols include:
- Immediate notification to adjacent facilities
- Coordination with local emergency services
- Deployment of specially trained personnel
- Implementation of state-of-the-art containment technology [6]
This all-encompassing approach delivers quick response times in critical situations. Automated safety features combined with emergency response protocols set new standards in lithium battery recycling safety. This supports environmentally responsible practices throughout the industry.
System Deployment Transforms Recycling Operations
Call2Recycle’s OneDrum solution has changed battery collection operations completely. The system cuts down preparation time for transport and recycling by 80% compared to traditional methods [7]. This breakthrough lets facilities handle large volumes of mixed consumer batteries quickly without chemical sorting or protecting individual terminals.
Streamlined Collection Process
OneDrum’s fresh approach lets collection sites put both single-use and rechargeable batteries in one container. This cuts storage needs by a lot [7]. The system helps municipalities and organizations handle more batteries without extra resources. The automated sorting system processes 500 kilograms of batteries every hour [8]. This doubles what conventional sorting lines can do.
Data Analytics Drive Efficiency
Machine learning algorithms and live monitoring have changed recycling operations through informed decision making. Smart sensors and hyperspectral cameras check items on conveyor belts and collect vital metadata to make processes better [9]. This information goes to cloud databases and trains machine learning models to boost waste recognition and sorting.
The system’s analytical capabilities show impressive results:
- Fuel costs dropped by 10%
- Task completion jumped by 24%
- AI predictions improved resource allocation [10]
The platform’s complete data analysis helps with:
- Better collection routes
- Quick schedule changes
- Live bin fill monitoring
- Smart maintenance planning
The National Renewable Energy Laboratory’s battery recycling supply chain analysis shows recycled consumer battery scrap could become a key source of raw materials for U.S. manufacturing [11]. This makes supply chains stronger for U.S. battery makers, and automated sorting works particularly well for cobalt recovery before 2035 [11].
The system’s data-driven approach sets new standards in operational efficiency. Collection sites work faster and use resources better [10]. Small changes in operations, like magnetic field strength and flotation cell time, have improved battery material separation by a lot [8].
Technology Paves Way for Sustainable Future
Studies show that lithium-ion battery recycling creates less than half the greenhouse gas emissions compared to conventional mining and refinement [12]. Advanced recycling methods give valuable materials like lithium, cobalt, and nickel a second life in manufacturing processes. This establishes a reliable circular economy for battery components.
Environmental Impact Metrics
Stanford University’s lifecycle analysis shows that battery recycling uses about one-fourth of the water and energy compared to traditional mining operations [12]. In fact, manufacturing scrap recycling brings even more environmental benefits by generating just 19% of mining’s greenhouse gas emissions [12].
Recycled batteries travel an average of 140 miles, which stands in stark contrast to the 35,000-mile experience needed for conventionally mined and refined metals [12]. Modern recycling facilities use cleaner energy sources among other benefits. They incorporate hydropower, geothermal, and solar energy in their operations.
Scaling Potential Across Markets
The lithium battery recycling market shows remarkable growth potential. Projections suggest 15 million metric tons of spent batteries by 2030 [13]. Right now, only 5% of lithium batteries get recycled [14]. This presents substantial opportunities to expand the market.
Key factors driving market growth include:
- Recovery of up to 95% of battery components through innovative hydrometallurgical processes [15]
- Reduction in virgin material extraction pressures
- Strengthened domestic supply chains for battery manufacturers
- Improved program convenience for collection sites
Electric vehicles’ rapid adoption creates both challenges and opportunities to manage end-of-life batteries responsibly [15]. The recycling network grows through strategic collaborations with manufacturers like Chervon, Husqvarna, and Stanley Black & Decker [16]. These collaborations ensure easy access to recycling solutions that support sustainable battery ecosystems.
The industry faces rising lithium demand that could increase twentyfold by 2050 [17]. Notwithstanding that, recycling facilities now recover nearly all cobalt and nickel, plus over 80% of lithium from used batteries [17]. This quick recovery process makes recycling a vital component to meet future battery material needs.
Conclusion
Call2Recycle’s smart battery collection system is revolutionizing sustainable battery recycling. The system processes 500 kilograms of batteries every hour with advanced X-ray technology and automated sorting. Safety remains the top priority with live monitoring and emergency protocols that protect lithium batteries throughout the recycling process.
This informed approach has revolutionized recycling operations. The transport preparation time dropped by 80% while the sorting line output doubled. Smart sensors paired with machine learning algorithms have optimized collection routes. These improvements led to lower operational costs and reduced environmental effects.
Large Power leads the lithium battery industry and plans to expand these recycling capabilities worldwide. We want to create a quick and flexible worldwide network through mutually beneficial alliances with end-product manufacturers. This network will promote green practices and resource conservation.
The environmental advantages are clear. Battery recycling produces less than half the greenhouse gasses compared to conventional mining. It recovers up to 95% of battery components. These numbers show why recycling is a vital solution to meet the projected twentyfold increase in lithium needs by 2050.
Keep up with our latest ESG initiatives and battery recycling progress on Large Power’s website. We share updates about sustainable battery solutions and environmental protection regularly. Let’s work together to create a cleaner future for battery technology.