Contents
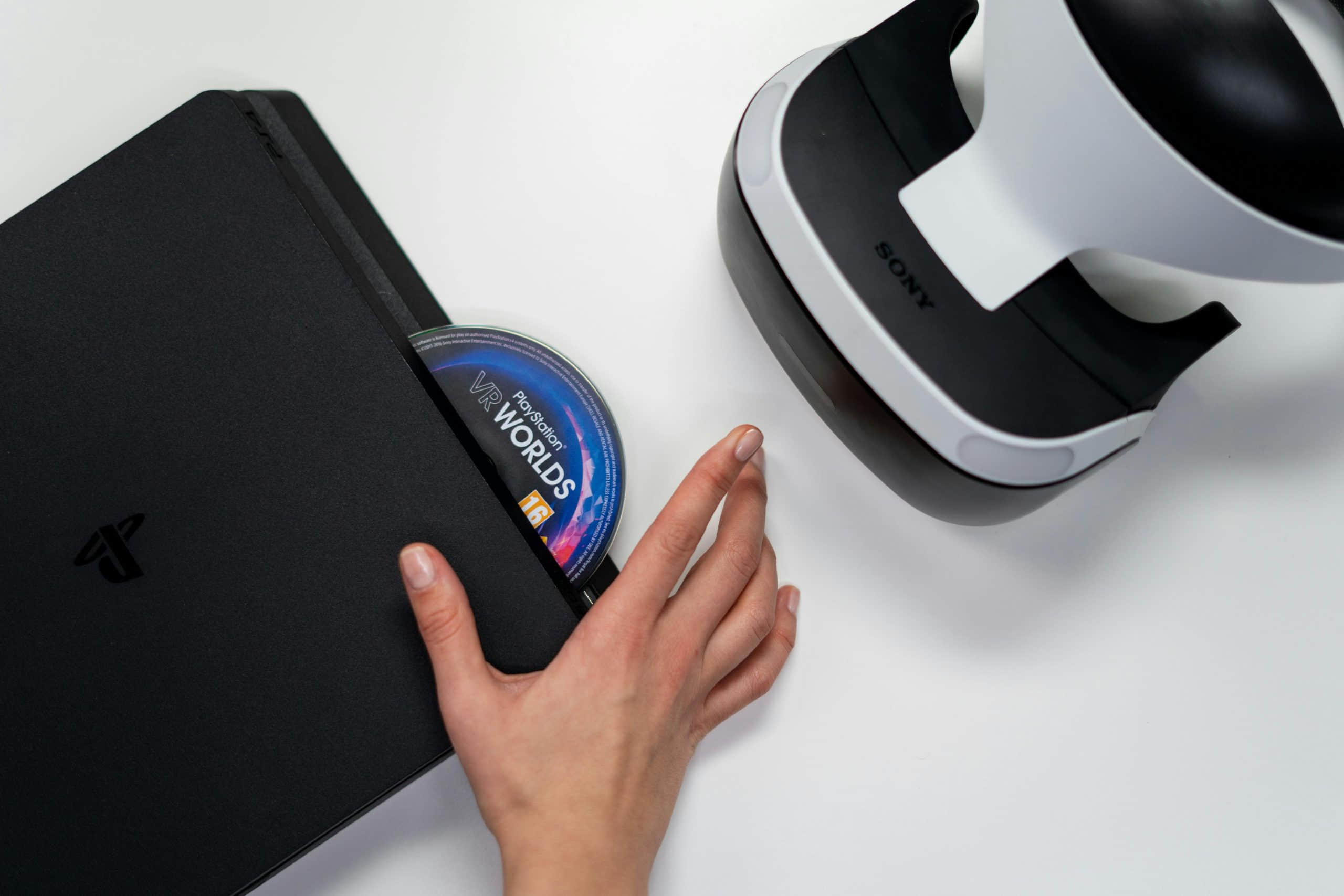
Battery pack manufacturers have spent over five decades mastering custom designs that power critical OEM devices. Their expertise dates back to 1965. Custom battery packs need to match five key requirements: shape, capacity, C-Rate, temperature, and voltage. These requirements make the design process technically challenging.
Custom battery packs play a crucial role in defense, aerospace, medical, and industrial applications of all types. These specialized power solutions need 4 to 12 weeks of development time. The results are worth the wait – they provide longer runtime, better efficiency, and improved reliability. These packs last 2 to 5 years or 300 to 500 charge cycles. They make the best use of available space and perform optimally in devices with complex shapes.
This piece explores the technical details of designing custom battery packs for complex shapes. We’ll look at core parameters, manufacturing methods, and testing protocols.
Core Design Parameters for Complex Battery Shapes
Battery pack design for complex shapes starts with three basic parameters that determine how well they perform and how safe they are. These parameters are the foundations for building reliable power solutions that fit naturally into irregular shapes.
Calculating Power Density Requirements
Power density tells us how fast a battery can deliver or receive energy per unit of volume, measured in watts per kilogram (W/kg). Lithium-ion batteries pack quite a punch with power density ranging from 150-220 Wh/kg[1]. This makes them perfect for uses that need quick energy delivery. The battery packs’ voltage comes from the chemical potential difference between cathode and anode, and the electrolyte’s electrochemical potential window affects it too [1].
The size and spread of particles affect the battery’s performance by a lot. When particles are smaller, Li+ ions don’t have to travel as far and face fewer diffusion barriers [1]. All the same, this comes with a catch – smaller particles mean more surface area, which could lead to extra side reactions and heat problems [1].
Thermal Management in Irregular Geometries
Heat management becomes crucial when designing custom battery packs. Engineers can study battery cooling through analytical solvers or number-crunching tools like Computer-Aided Engineering (CAE) and Computational Fluid Dynamics (CFD) software [1]. works best for big battery packs because it conducts heat better Liquid-cooling technology[2].
The Battery Thermal Management System (BTMS) keeps temperatures safe through:
- Active cooling methods that need extra equipment
- Passive cooling that offers a simpler setup with better cooling results [2]
Phase change materials (PCMs) are vital for passive cooling systems. They soak up battery heat at specific transition points without using extra energy [2]. Recent advances focus on mixed PCMs that use materials like expanded graphite and metal foam to make them stronger and better at conducting heat [2].
Structural Integrity Analysis
Structural integrity tests make sure battery packs stay reliable under different mechanical stresses. Three-point bending tests help assess various pouch battery setups, while finite element models show how stress spreads and where short circuits might happen [3]. Folded configurations and pouch casing make batteries much stronger – 14 and 30 times stronger to be exact [3].
Today’s enclosures come with sensors that watch battery health and give mechanical support, especially in dynamic conditions [3]. These enclosures must handle frequencies above 300 Hz during complete vibration testing [3]. The design process also thinks over what happens when the battery faces maximum strain during braking, sharp turns, and vertical impacts [3].
Lithium-ion battery packs need a design platform that brings together many disciplines. These systems combine specific architecture, electrical schemes, controls, sensors, and management systems [1]. On top of that, newer design methods combine batteries with structural parts more often. Cell-To-Pack (CTP) and Cell-To-Chassis (CTC) approaches show this trend, and they help cut manufacturing costs [1].
Advanced Cell Configuration Techniques
Battery pack design for complex shapes needs proper cell configuration. The way cells line up affects performance, safety, and how well the space gets used in the final design.
Parallel vs Series Arrangements for Curved Surfaces
Specific voltage and capacity needs determine whether to use series or parallel configurations on curved surfaces. Series connections work like a chain – positive terminals link to negative ones to boost voltage output [4]. Parallel setups keep voltage steady but boost total capacity by joining positive terminals together and negative terminals together [4].
Let’s look at a real example. Two 12V 100Ah batteries in series give you 24V with 100Ah capacity. Put these same batteries in parallel and you’ll get 12V but double the capacity to 200Ah [5]. This gives designers room to match power delivery to what their devices need.
Series arrangements bring clear benefits for complex shapes:
- Higher voltage output in less space
- Smaller conductor size needs
- Better power delivery efficiency [4]
Series setups do have their drawbacks. One bad cell can shut down the whole system. Some newer packs use solid-state switches that can bypass faulty cells [4].
Cell Spacing Optimization
The right cell spacing makes a big difference in heat management and structural strength. Studies show smart spacing can cut maximum temperature differences by over 60%[6]. Engineers use computer fluid simulations to find the best spacing patterns that cool better without taking up too much space.
Cell spacing needs to balance several things:
- Heat removal needs
- Structural support
- Room for cooling or heating equipment [7]
New research shows uneven gaps between cells can keep temperatures more uniform than equal spacing [6]. The process looks at different air flow rates to make sure cooling works well in all conditions [6].
Curved surfaces need extra attention to spacing. Designers must balance:
- Cooling efficiency
- Physical stability
- Space use
- Room for sensors [8]
Modern manufacturing, especially 3D printing and designs inspired by nature, gives precise control over cell spacing in tricky shapes [8]. These methods help right onto curved surfaces to use space better build stacked cells[8].
Getting cells arranged right depends on keeping components dry, lining up electrodes, and controlling pressure [9]. You need to position everything within 1-2mm on each edge during assembly [9].
Custom Battery Pack Manufacturing Methods
Manufacturing custom battery packs needs exact engineering and advanced automation techniques. Modern manufacturing methods combine 3D printing technology, automated assembly systems, and strict quality control. These methods make sure the batteries perform well and stay safe.
3D-Printed Housing Design
3D printing technology helps produce with high-aspect-ratio architectures geometrically complex battery housings[10]. This method gives better shape conformability and adjustable dimensions that lead to improved areal energy densities [10]. The housing design protects battery cells from environmental factors such as temperature changes, humidity, and water entry [11].
The process needs detailed 3D models that consider:
- Internal support structures
- Cooling system integration
- Cell placement optimization
- Access points for maintenance
Automated Cell Placement Systems
Robotic assembly lines with advanced vision systems place components with precision. These systems sort, stack, and weld cells with consistent accuracy [12]. Computer-controlled mechanisms ensure . They use calibration software to fix frame inaccuracies exact positioning within 10-20 micrometers[13].
The automation process includes these key elements:
- High-speed linear motors for five-axis positioning
- Temperature-controlled manufacturing environments
- Integrated vision analysis software for quality verification
- Automated sensor placement systems
Quality Control Checkpoints
Quality checks happen throughout manufacturing, from material inspection to final pack validation. Cell testing checks state of health, capacity, charging rates, and mechanical stress tolerance [14]. Test rigs run repeated cycles that include charge-discharge tests and thermal analysis [12].
The manufacturing process has three distinct quality control phases [15]:
- Incoming Quality Control (IQC)
- Verification of cell capacities and voltage profiles
- Component inspection including plates, foils, and separators
- Circuit board defect analysis
- In-Process Quality Control (IPQC)
- Statistical process control tracking
- Cell and pack inspection at each assembly stage
- Continuous process audits
- Final Product Quality Control (FPQC)
- Dimensional inspection against specifications
- X-ray examination of internal connections
- Functional testing under various load conditions
Modern quality control systems use AI algorithms to analyze images and sensor data. These algorithms detect anomalies and allow quick corrections [12]. Manufacturers track key performance metrics through statistical analysis to maintain strict process controls [15].
BMS Integration for Non-Standard Shapes
Battery Management Systems (BMS) integration brings unique challenges when working with non-standard shaped battery packs. Engineers must pay close attention to sensor placement and thermal monitoring strategies. A BMS’s performance directly affects how long batteries last, how well they work, and how safe they are in complex shapes.
Sensor Placement Strategy
Placing sensors on irregular surfaces needs a systematic approach that balances physical limits and measurement precision. Research shows that sensor positions with lower incidence angles produce better results [2]. The placement strategy has two main goals:
- Making single reference position uncertainty as small as possible
- Mixing uncertainty reduction with range-based positioning
Sensors need to stay a few centimeters apart to work properly and account for their size [2]. This space between sensors, called the guard area, will give accurate data without sensors interfering with each other.
Advanced placement algorithms use multi-objective memetic optimization to balance:
- Measurement quality based on acoustic signal incidence angles
- Information from different sensor setups
- Physical limits of irregular surfaces
Heat Distribution Monitoring
Temperature monitoring plays a vital role in BMS integration and directly affects battery performance and safety. Studies show that battery pack cores run about 2°C hotter than outer sections. These differences can reach tens of degrees in bigger modules [16].
The thermal management system works with both active and passive technologies:
Active Components:
- Fans and pumps that need external power
- Temperature adjustments as they happen
- Better control of heat conditions
Passive Elements:
- Heat sinks and pipes that work without power
- Materials that conduct heat well
- Cooling through natural air flow
Modern BMS designs include sophisticated monitoring features [18]:
- Up-to-the-minute state of charge (SOC) evaluation
- State of health (SOH) characteristic tracking
- Ongoing impedance estimation
- Performance capacity monitoring
The system adapts to slow and fast temperature changes since most research only looks at steady temperatures [18]. That’s why advanced BMS designs now come with multi-level safety protocols and backup protection circuits [19].
Heat distribution monitoring depends on precise sensor networks that track thermal patterns throughout the battery pack. Each cell’s jelly roll structure shows different heat conductivity in different directions, with less conductivity radially [16]. This means sensors must be placed strategically for accurate temperature mapping.
The monitoring system keeps temperatures at their best levels since changes can greatly affect performance. The BMS analyzes data continuously to spot early signs of thermal runaway and take preventive action [19].
Testing and Validation Protocols
Strict testing protocols help custom battery packs meet safety and performance standards in a variety of operating conditions. These validation procedures check mechanical durability, thermal resilience, and compliance with international regulations.
Vibration Testing for Complex Geometries
plays a crucial role in validating battery packs with irregular shapes. Tests cover both fixed-frequency and sweep-frequency vibrations that simulate real-life vehicle conditions Random vibration analysis[20]. Power spectral density measurements help assess energy distribution across frequency ranges. Root mean square acceleration values stay within specified limits [20].
Today’s vibration testing platforms feature:
- Signal generators producing sweep signals
- Power amplifiers driving mechanical vibrators
- High-speed data collectors recording acceleration measurements
- Laser Doppler vibrometers tracking surface movements [3]
Studies show mechanical vibration durability affects internal battery structures heavily. Computer tomography analysis of eighteen different 18650 battery types shows structural changes after random vibration loads [3].
Thermal Cycling Assessment
Battery performance under extreme temperature changes requires thermal cycling tests. Standard protocols specify these temperature ranges:
- IEC 62133: 75°C to 20°C to -20°C with 30-minute transitions [21]
- UL 2054: 70°C to -40°C with 30-minute transitions [21]
- UL 1642: 70°C to 20°C to -40°C with 30-minute transitions [21]
Modern thermal management systems keep temperature differences within 3 degrees across battery cells [22]. Optimized air intake holes help prevent temperature distribution problems caused by varying distances between batteries and cooling fans [22].
Safety Certification Requirements
Safety certification requires complete testing against multiple standards. UL 1642 for lithium cells, UL 2054 for nickel cells or lithium/nickel packs, and IEC 60086 series for various battery chemistries lead the way [23]. CTIA certification programs verify conformance to IEEE Standard 1725TM1-2006 for rechargeable batteries [23].
Quality control checkpoints during testing include:
- Visual inspections for defects
- Electrical measurements of voltage and current
- Mechanical stress evaluations
- Thermal performance assessments
- Chemical composition analysis [24]
Current thermal runaway prevention strategies use model-based warning methods, big data analytics, and multi-dimensional signal monitoring [1]. Direct current impedance measurements allow non-destructive assessment of battery thermal safety throughout operational lifespans [1].
Battery Management Unit (BMU) validation checks these critical functions:
- State-of-charge estimation accuracy
- Cell balancing capabilities
- Voltage monitoring precision
- Current measurement reliability
- Temperature monitoring responsiveness [25]
Conclusion
Custom battery pack design needs precise engineering expertise, detailed testing protocols, and advanced manufacturing capabilities. Engineers create reliable power solutions that fit naturally into complex shapes by carefully evaluating power density requirements, thermal management systems, and structural integrity analysis.
The latest cell configuration techniques help arrange batteries optimally in curved surfaces. Advanced manufacturing methods combine 3D printing technology with automated assembly systems. Battery Management Systems monitor heat distribution and keep operating conditions safe with strategic sensor placement.
Rigorous testing protocols ensure these custom solutions meet safety standards and performance requirements. The durability and reliability of each battery pack design is confirmed through extensive vibration testing, thermal cycling assessments, and safety certifications.
Large Power creates custom battery solutions that match unique project requirements. The company’s engineering team offers expert guidance and support to help with your custom battery pack design needs.
Custom battery pack design has grown into a sophisticated engineering discipline. Today’s manufacturers deliver high-performance power solutions that make the best use of space while ensuring peak performance in complex-shaped devices. These developments challenge traditional limits in defense, aerospace, medical, and industrial applications, with more innovative solutions on the horizon.
FAQs
Q1. What are the key considerations when designing a custom battery pack for complex shapes? The main considerations include calculating power density requirements, managing thermal issues in irregular geometries, ensuring structural integrity, optimizing cell configuration, and integrating an effective Battery Management System (BMS). Designers must also account for manufacturing methods and rigorous testing protocols.
Q2. How does 3D printing technology contribute to custom battery pack design? 3D printing enables the production of geometrically complex battery housings with high-aspect-ratio architectures. This technology offers enhanced shape conformability and tunable dimensions, resulting in improved areal energy densities and better protection for battery cells against environmental factors.
Q3. What role does the Battery Management System (BMS) play in non-standard shaped battery packs? The BMS is crucial for monitoring and managing battery performance, especially in complex geometries. It involves strategic sensor placement for accurate temperature mapping and state-of-charge evaluation. The BMS helps maintain optimal operating temperatures and can detect early warning signs of thermal runaway.
Q4. What testing procedures are essential for custom battery packs? Critical testing procedures include vibration testing for complex geometries, thermal cycling assessment, and safety certification requirements. These tests verify mechanical durability, thermal resilience, and compliance with international regulations. They typically involve random vibration analysis, extreme temperature variations, and comprehensive safety standard evaluations.
Q5. How do manufacturers ensure quality control in custom battery pack production? Quality control in custom battery pack manufacturing involves three main phases: Incoming Quality Control (IQC), In-Process Quality Control (IPQC), and Final Product Quality Control (FPQC). These stages include component inspections, continuous process audits, dimensional checks, X-ray examinations, and functional testing under various load conditions. Advanced systems also incorporate AI algorithms for anomaly detection.